Full Speed Ahead are a full line component producer whose products include handle bars, stems, chain sets, wheels, seat posts, stem caps and often one of their most well known products the headset, plus numerous other components. With more than 30 years of history behind them their parent company and production manufacturer TH Industries, their range of products has been put together with experience and testing based on what the market wants. Many of their products are specified as OEM on bikes that we can buy from major brands.
As part of their information and marketing process they invited us to their Taiwanese factories to have a look at the various products they make. We started off at the main headquaters in Taichung where they produce most of their CNC products and components kits. They also showed us around their research and development and testing laboratories, so we could have a full up close look at their supply chain.
The Factory
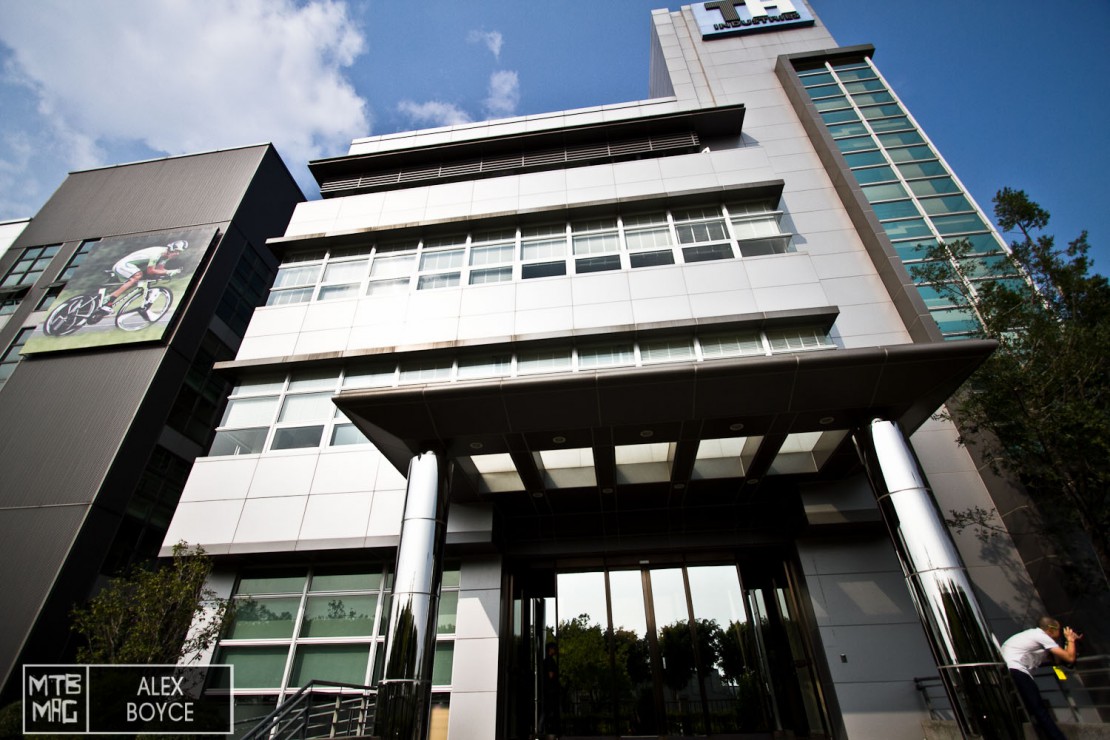
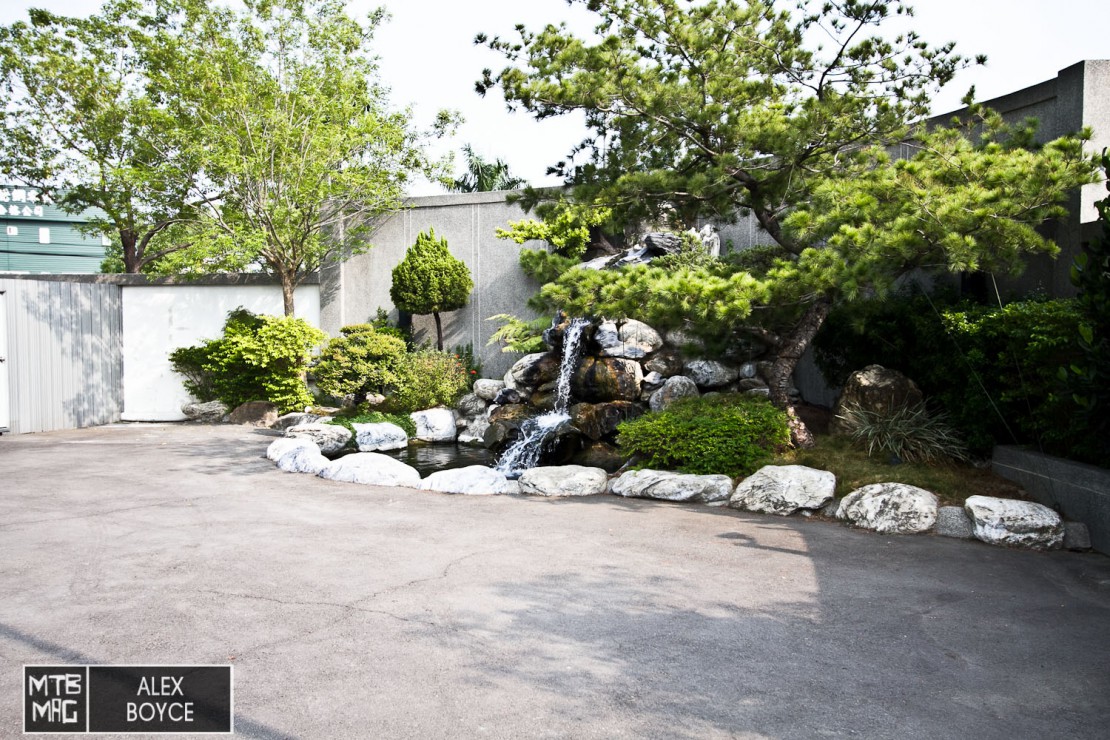
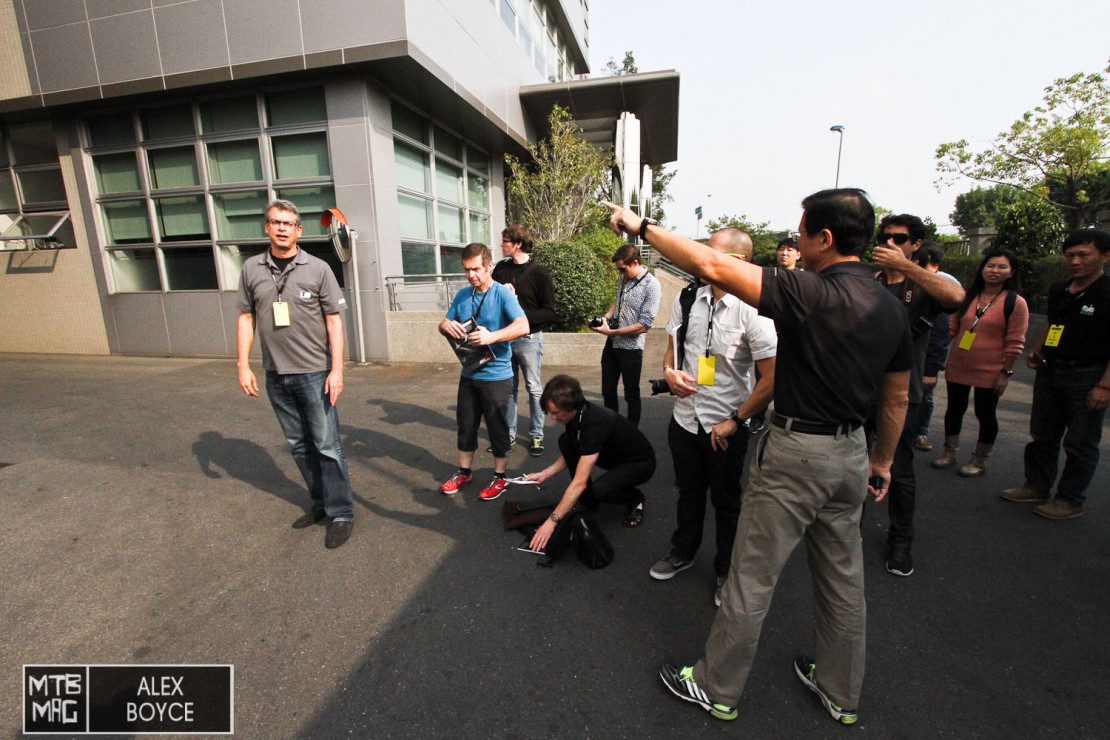
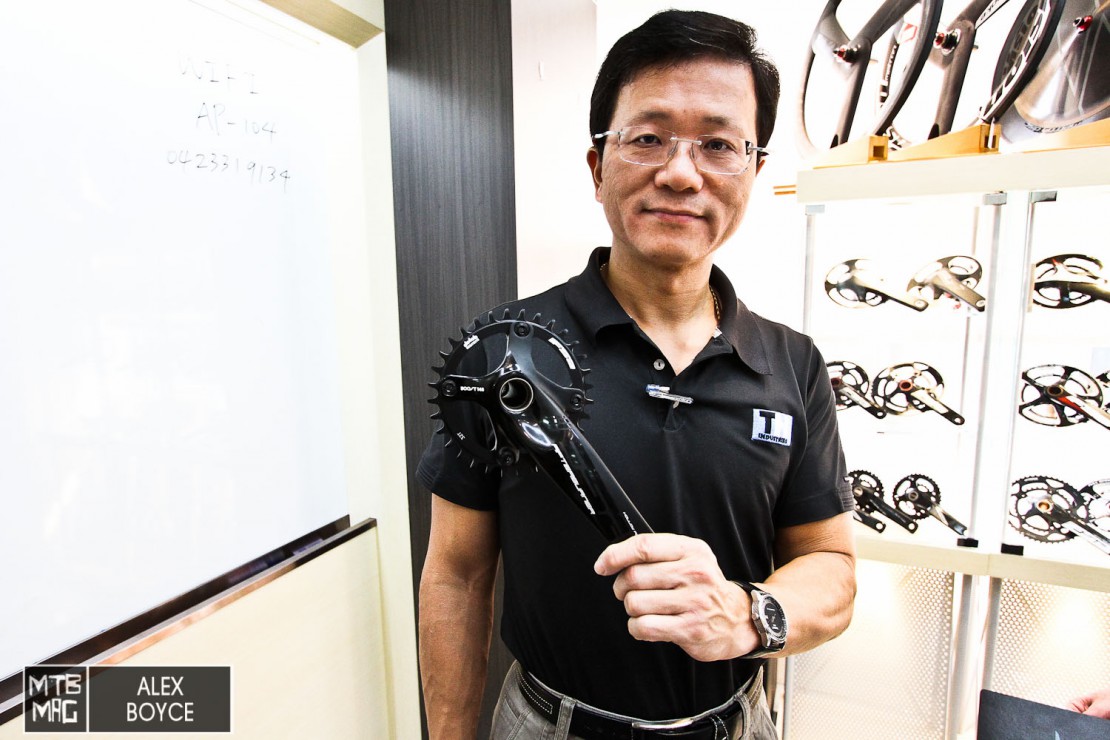
Production
FSA produce a large quantity of quality components across drive trains and parts and accessories, on state of the art production lines, we had a look around at the different processes going on, some things we could not show due to trade secrets, but what we saw was modern, set up to high safety standards that went beyond what local laws require and efficient. This facory receives the raw materials and then turns them into the things we use on the bike.
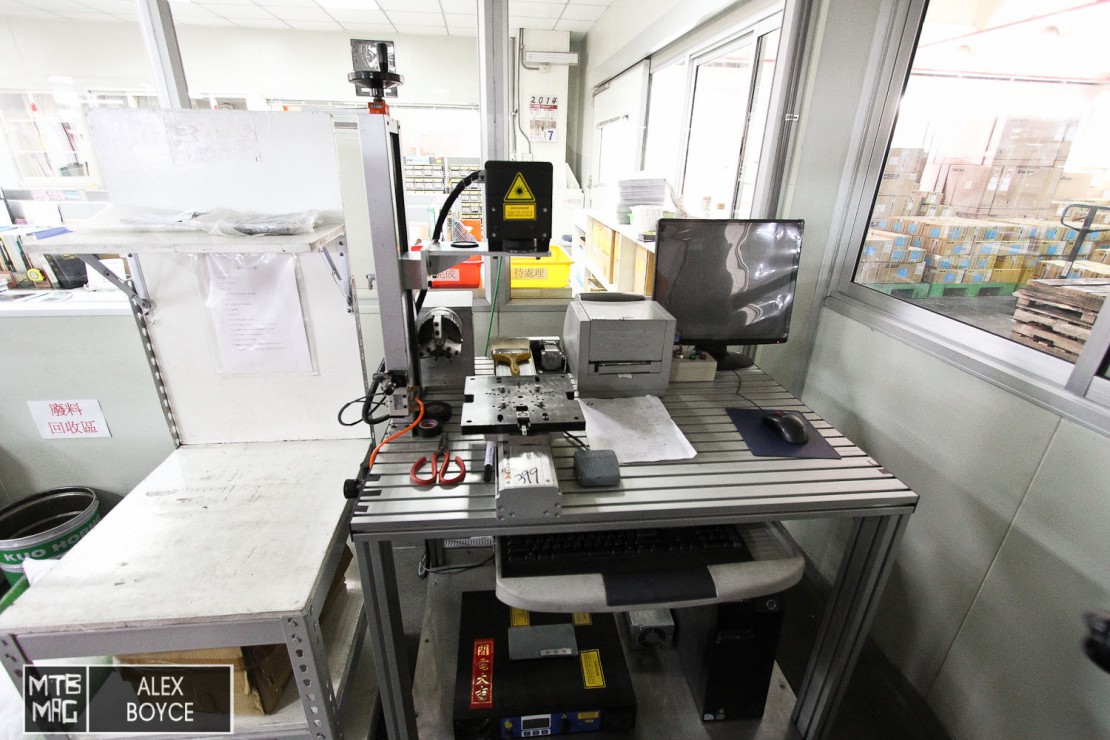
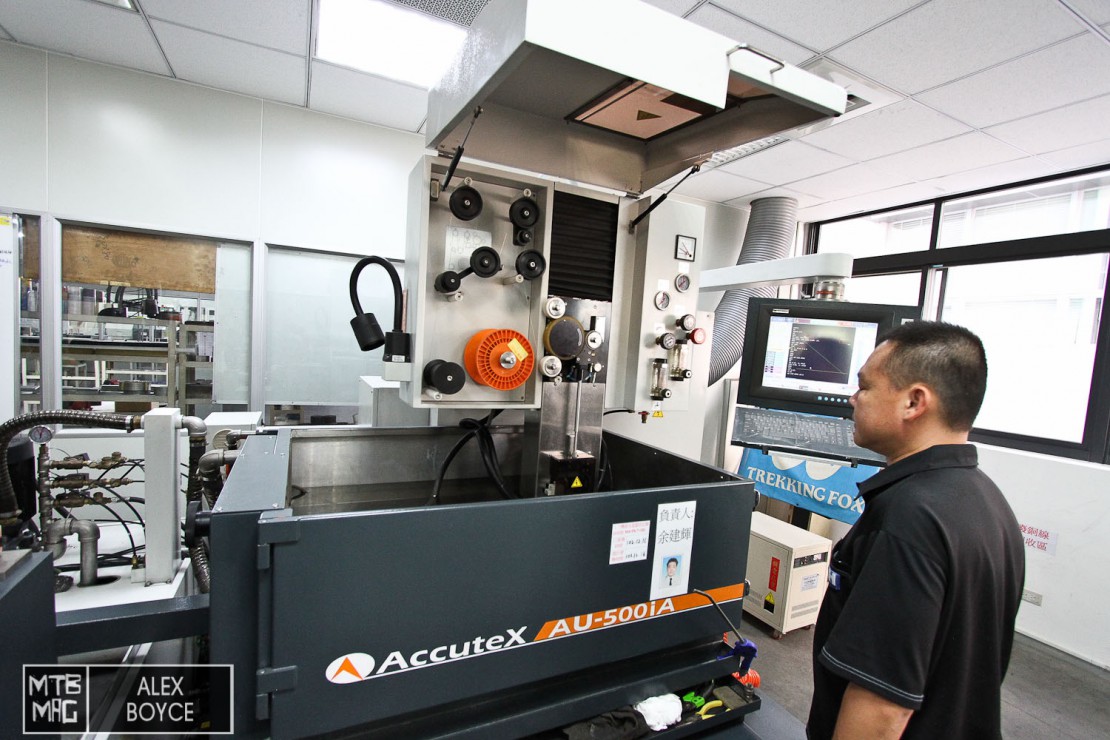
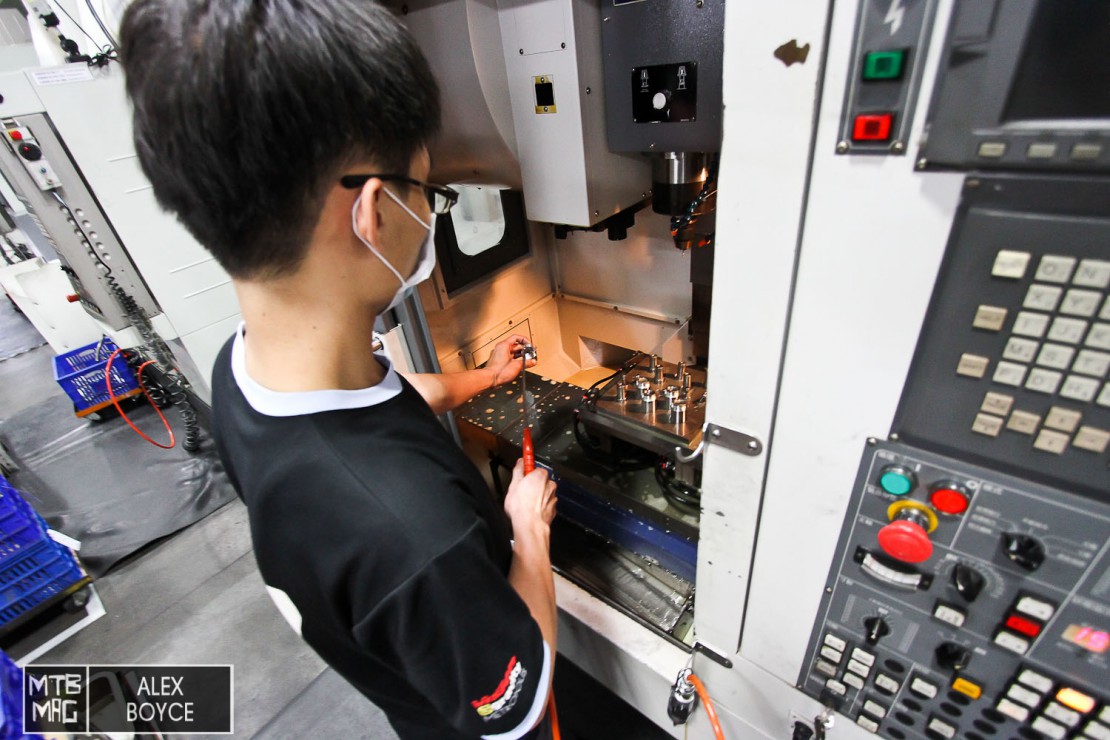
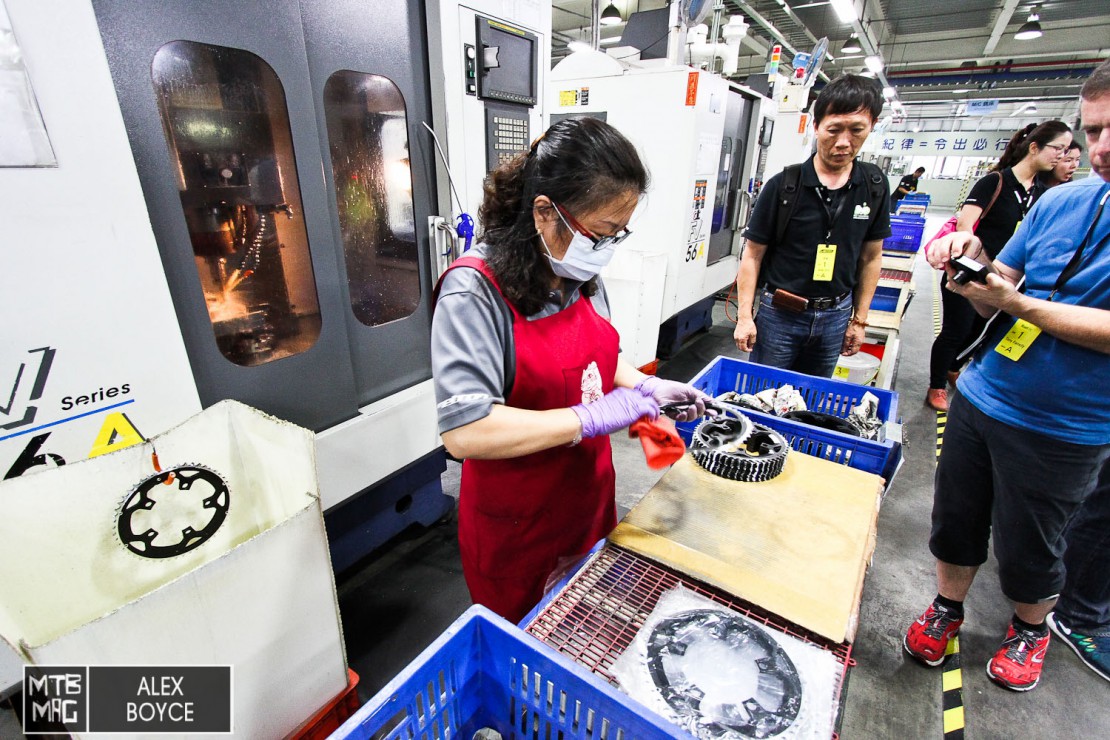
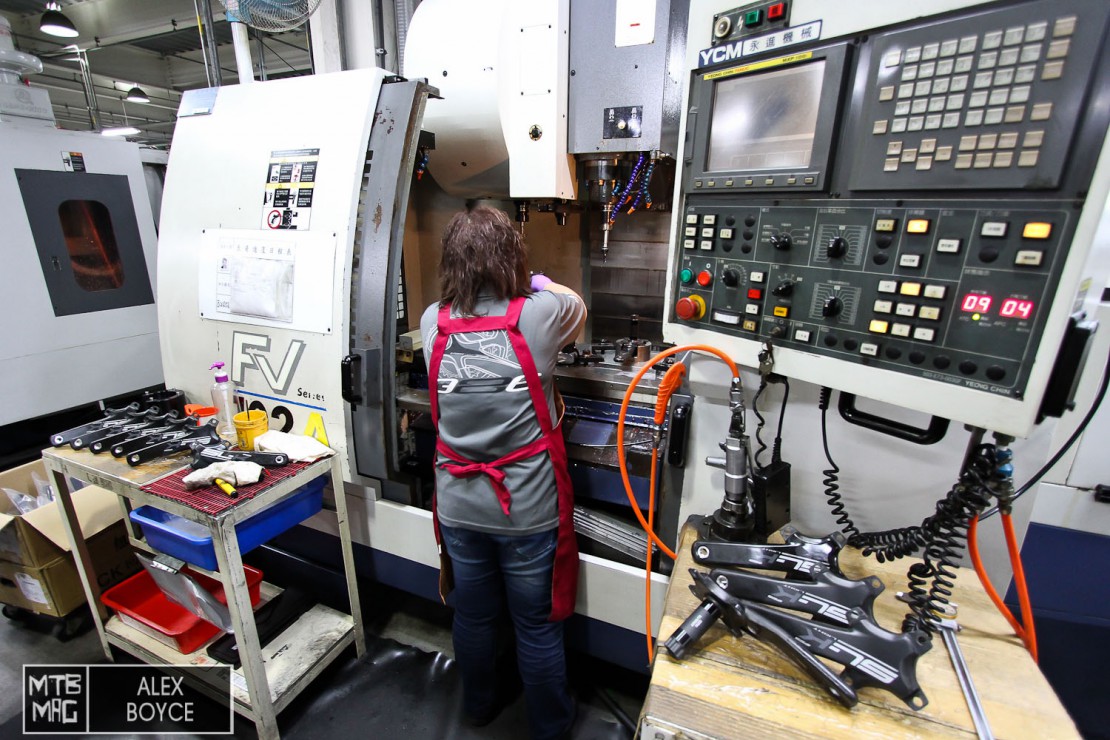
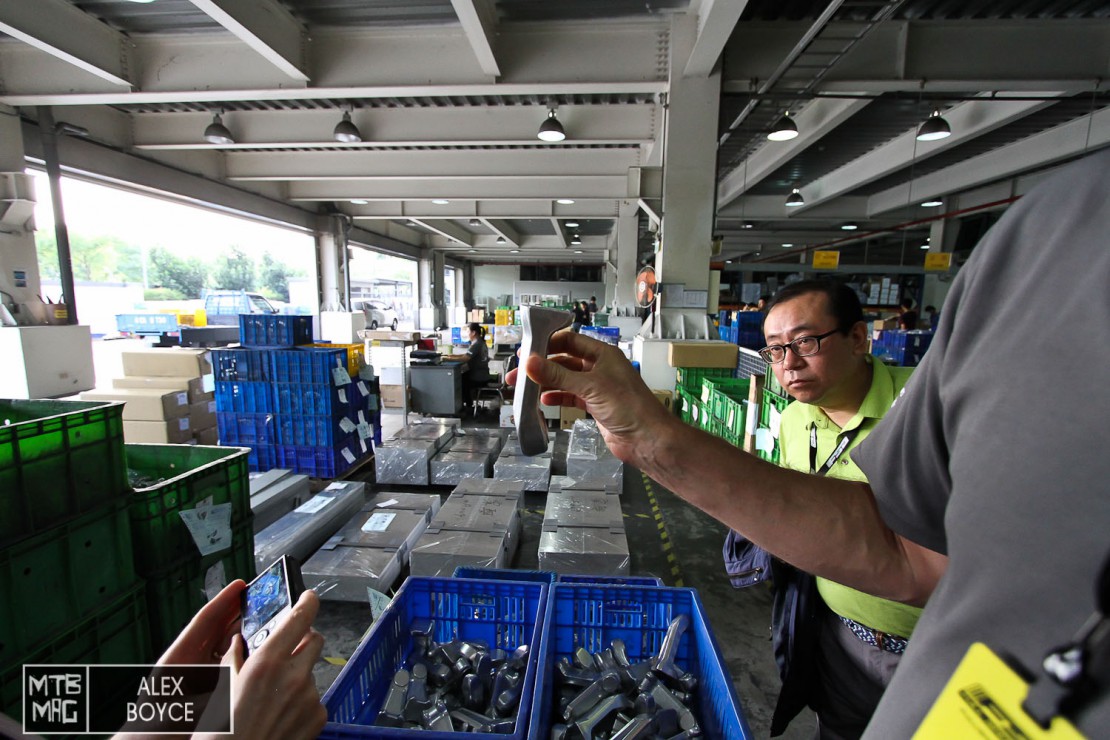
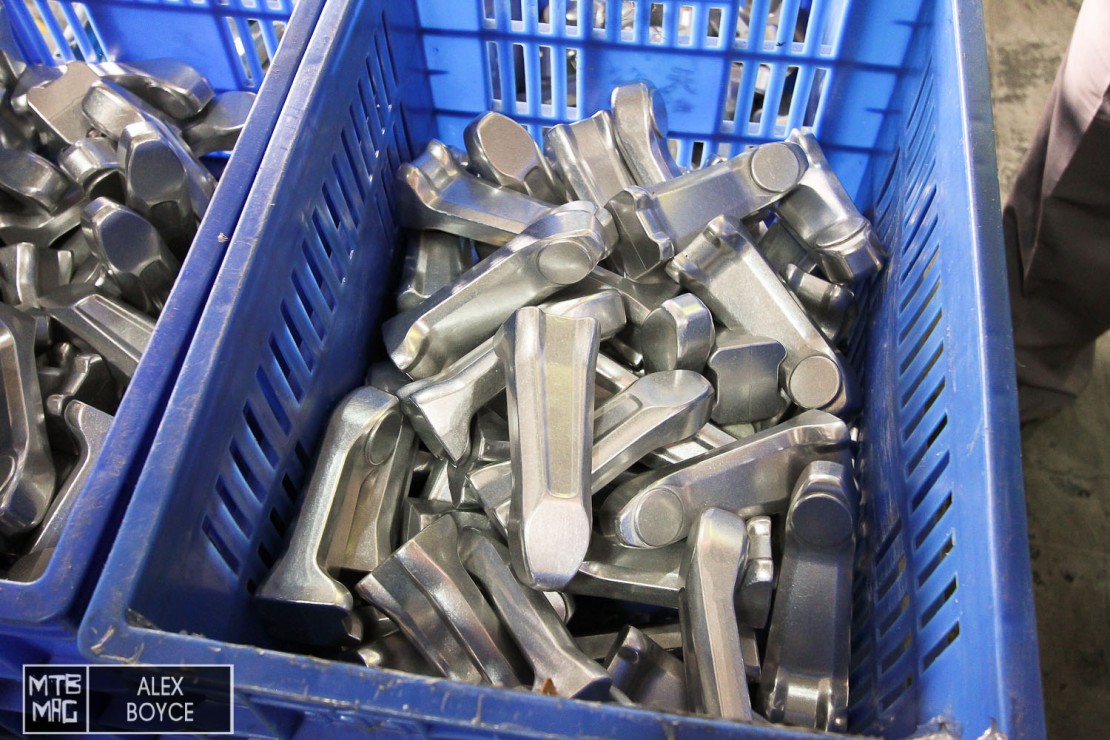
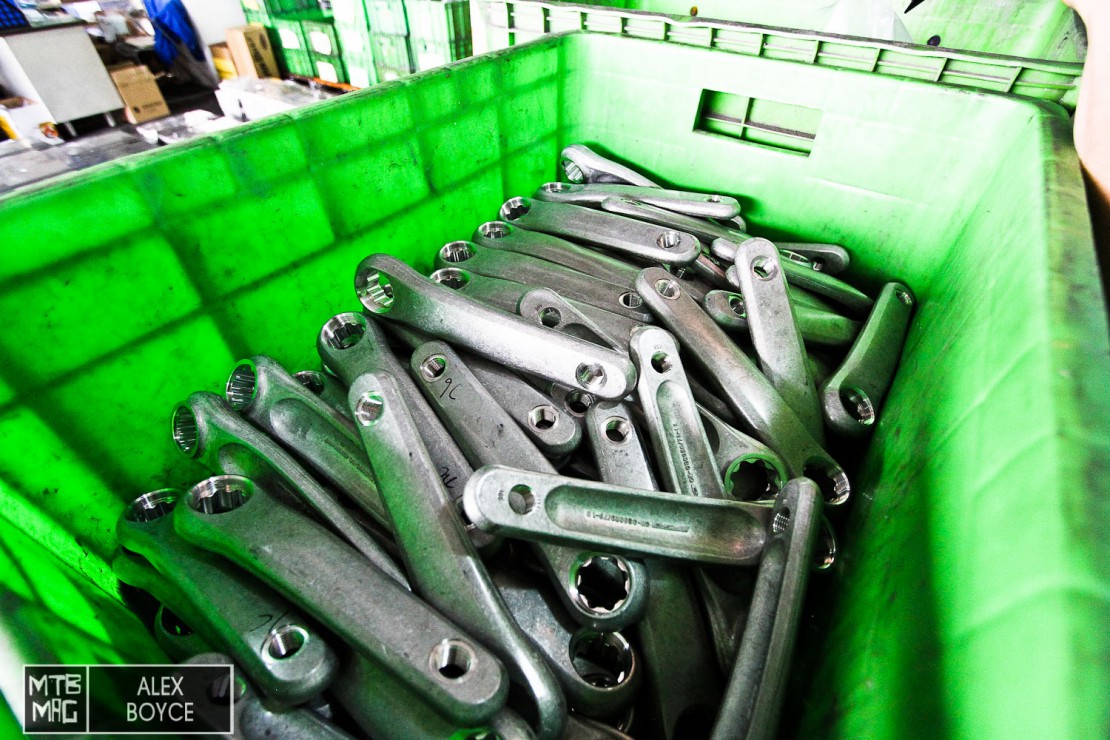
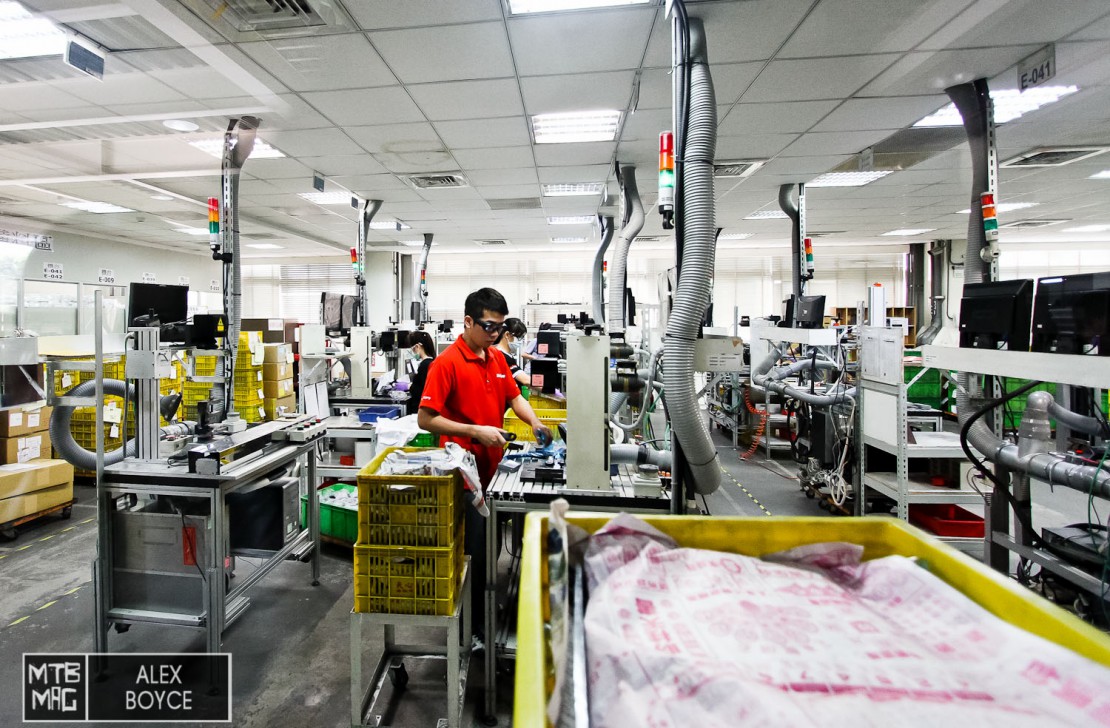
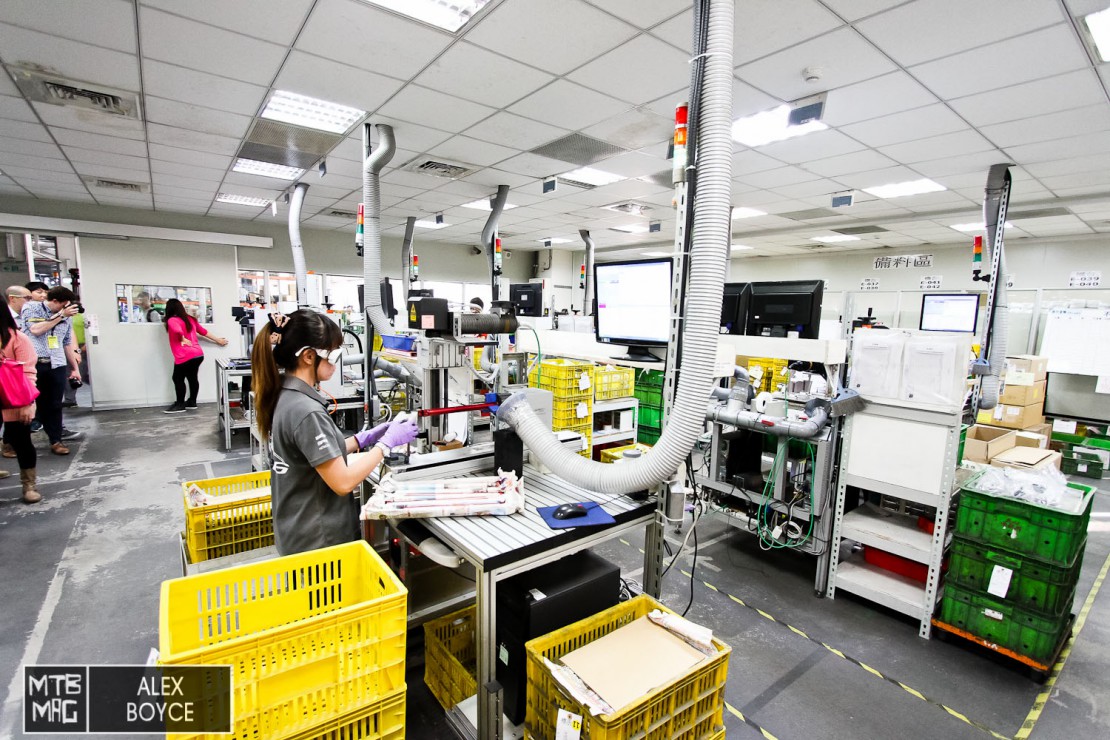
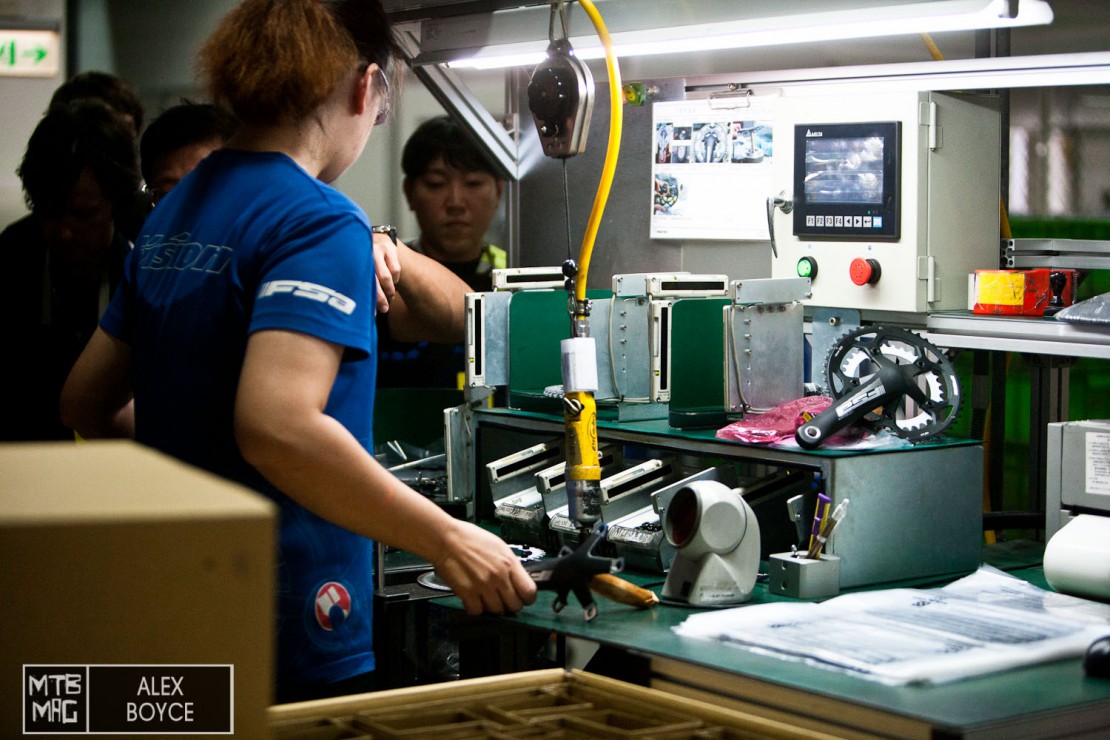
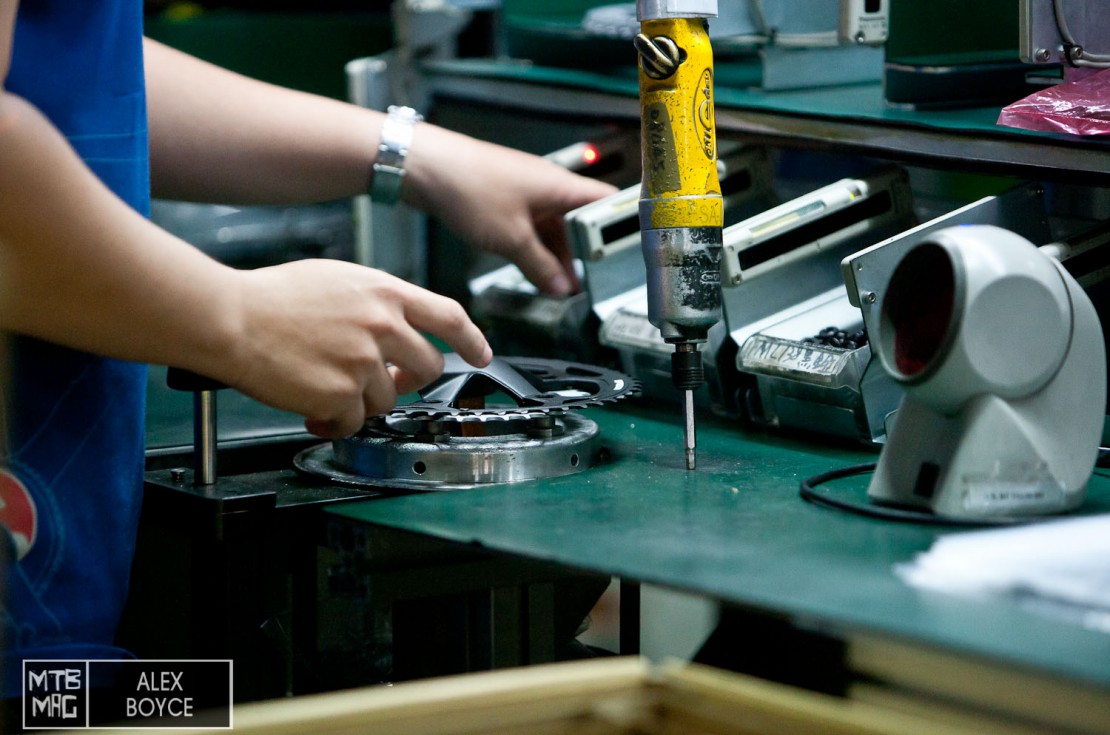

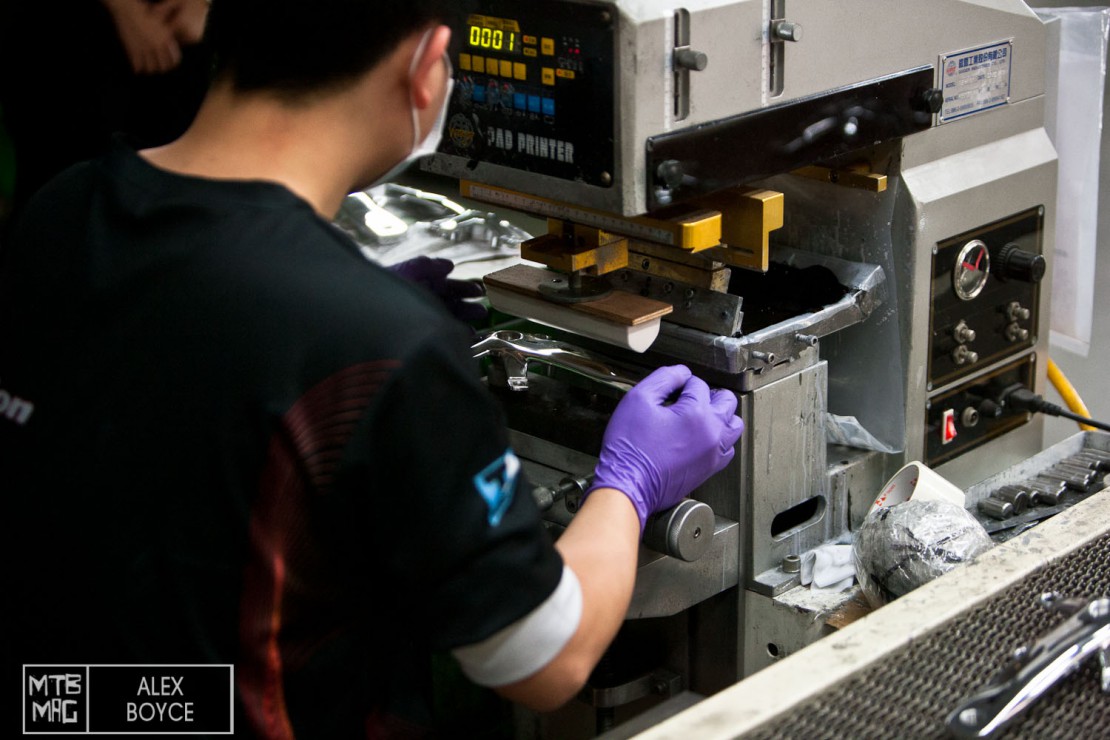
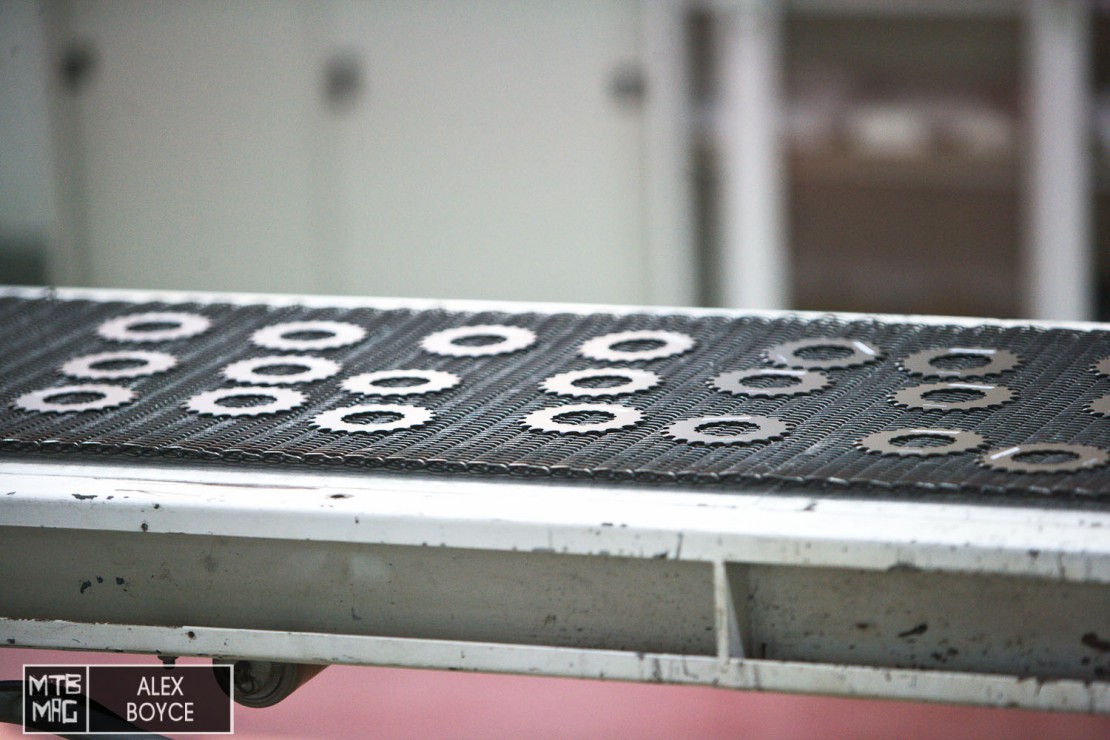
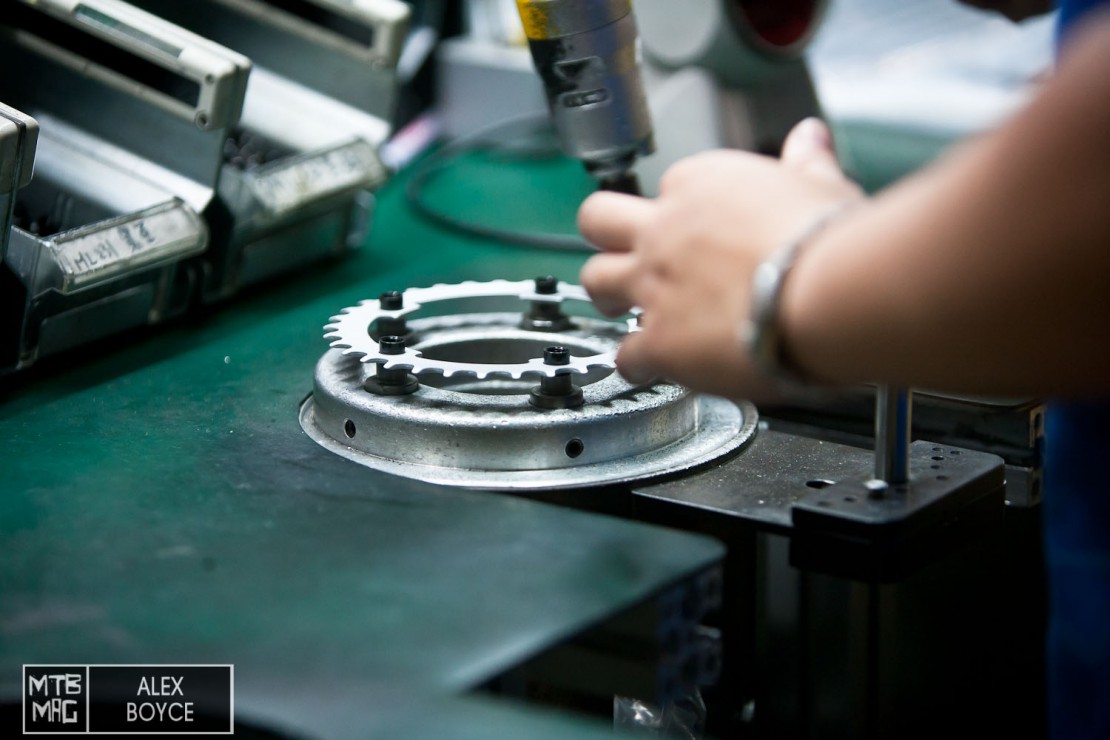
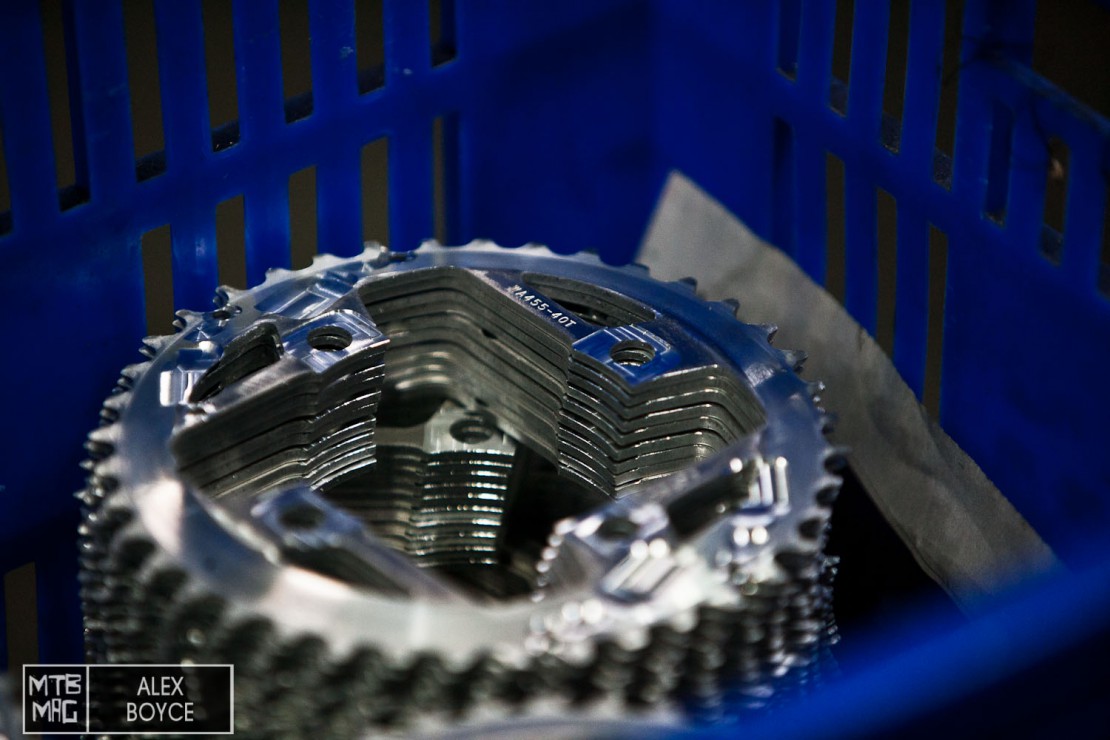
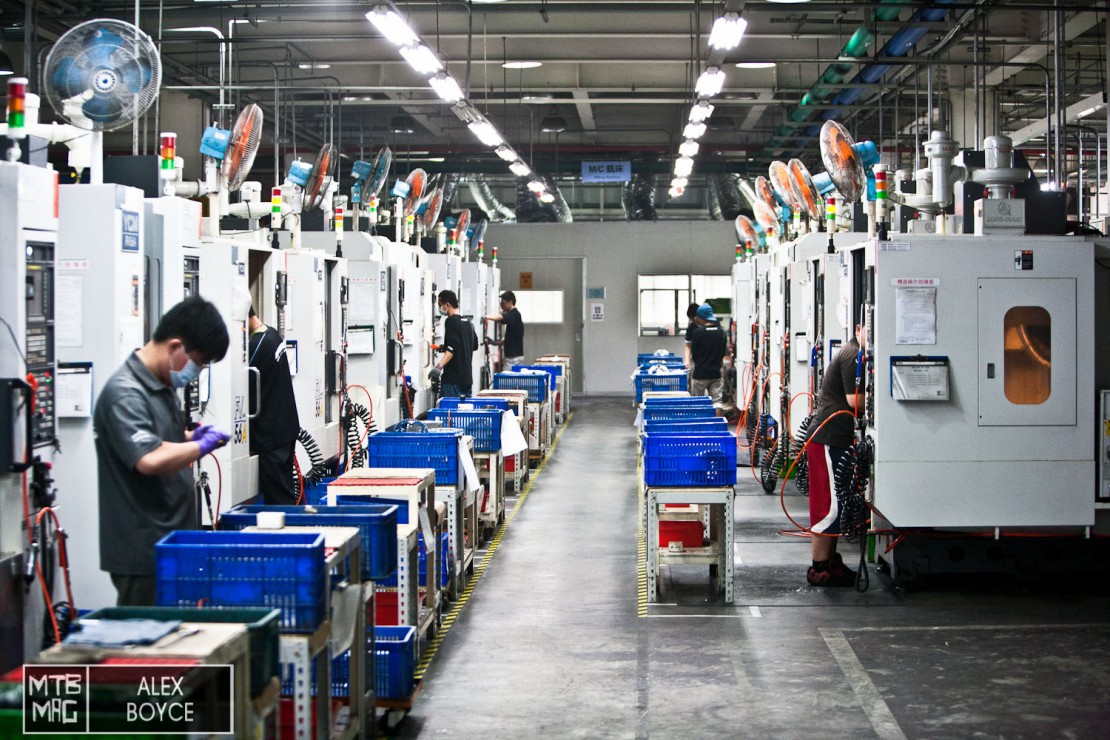
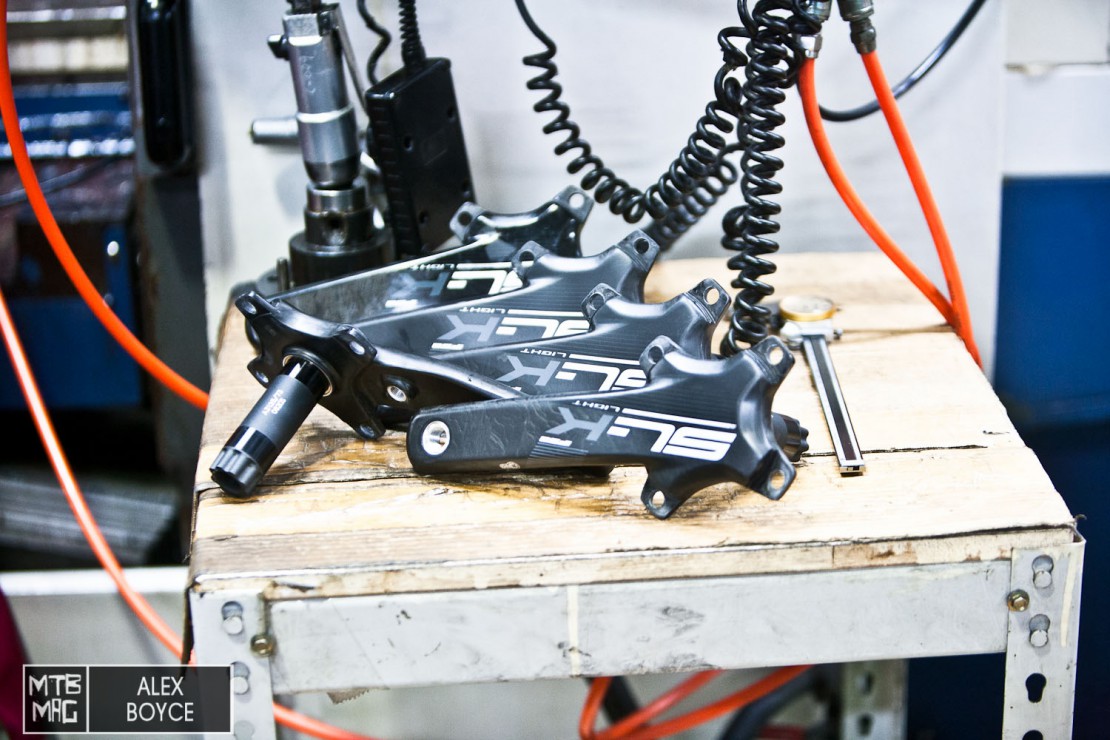
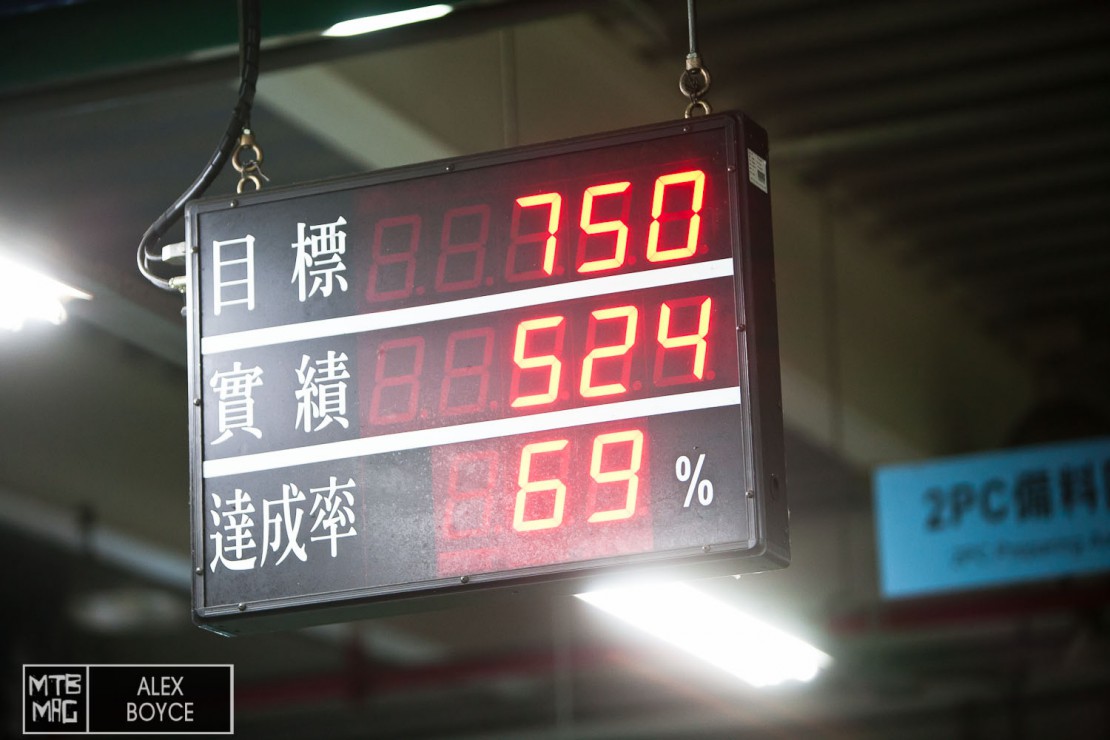
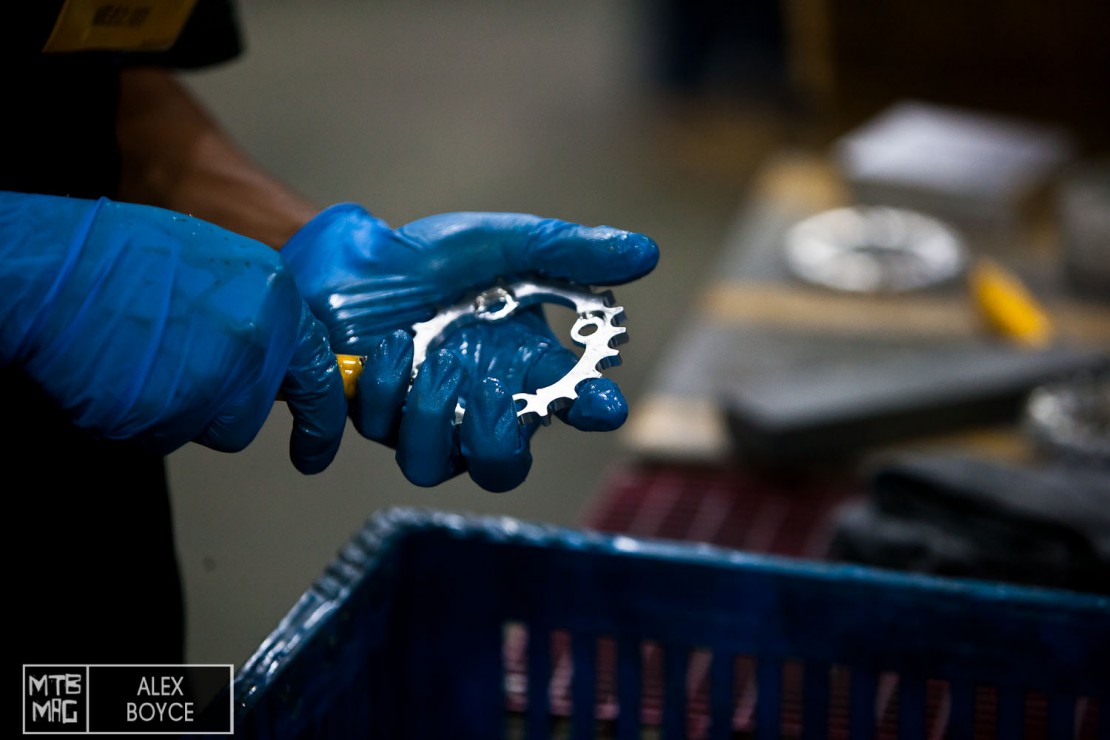
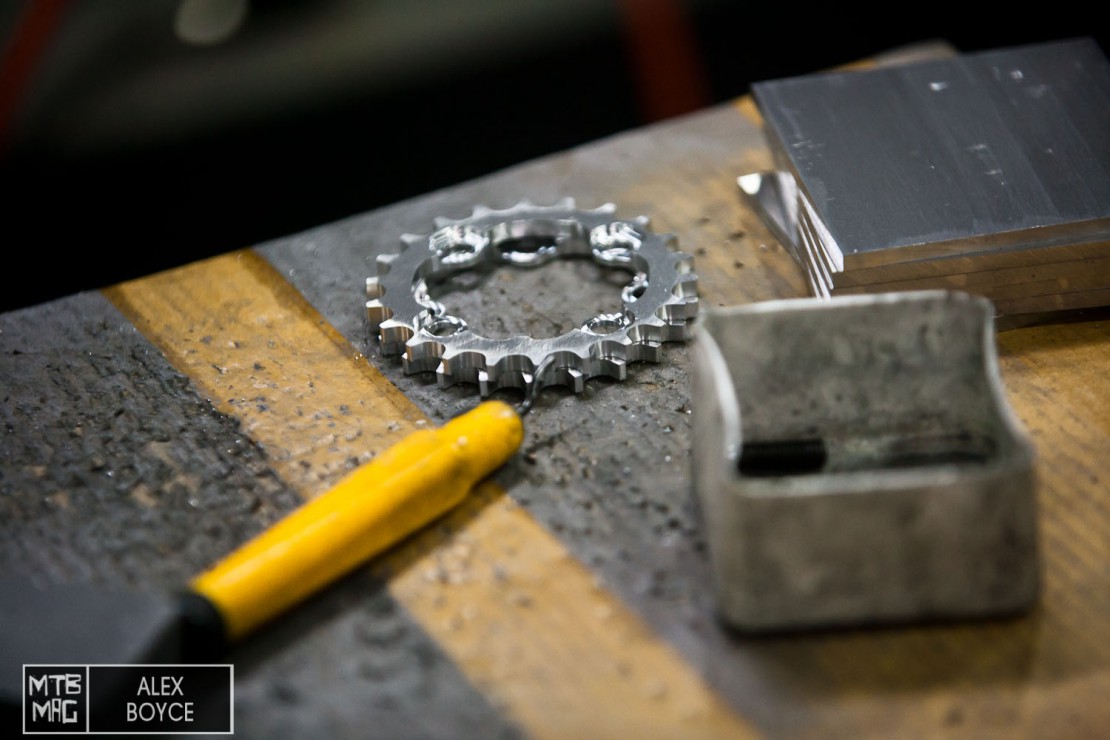
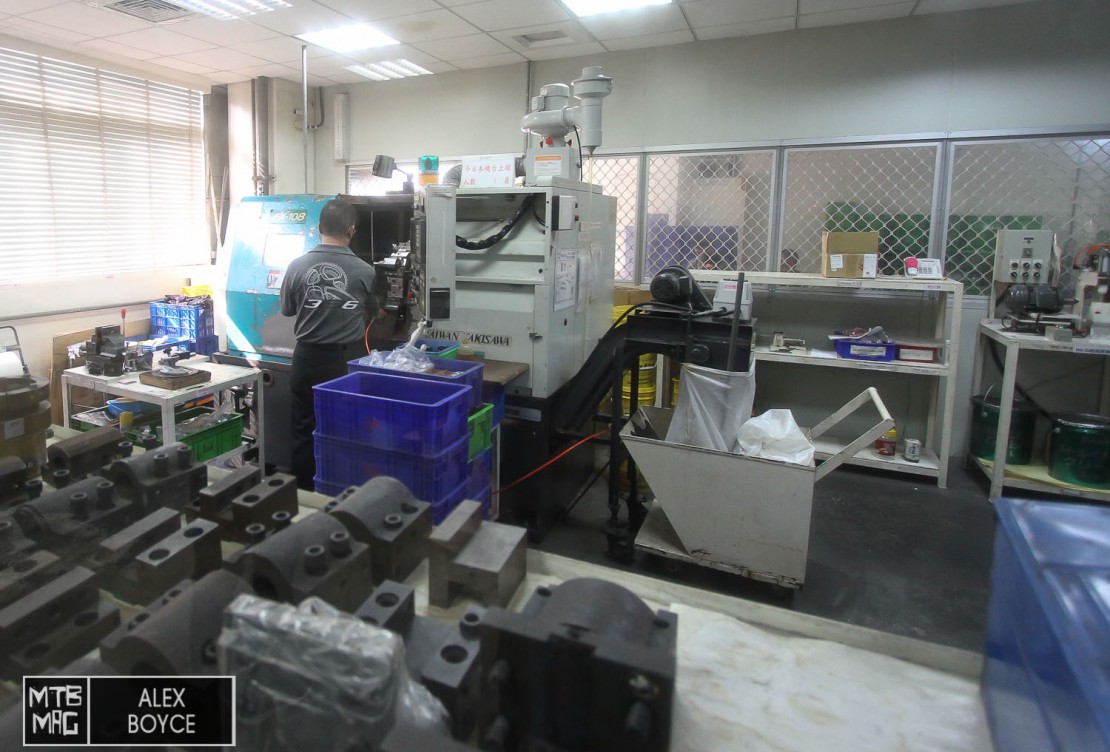
CNC
We though we would take a close up look at the CNC machines and some of the types of components that come out of them.
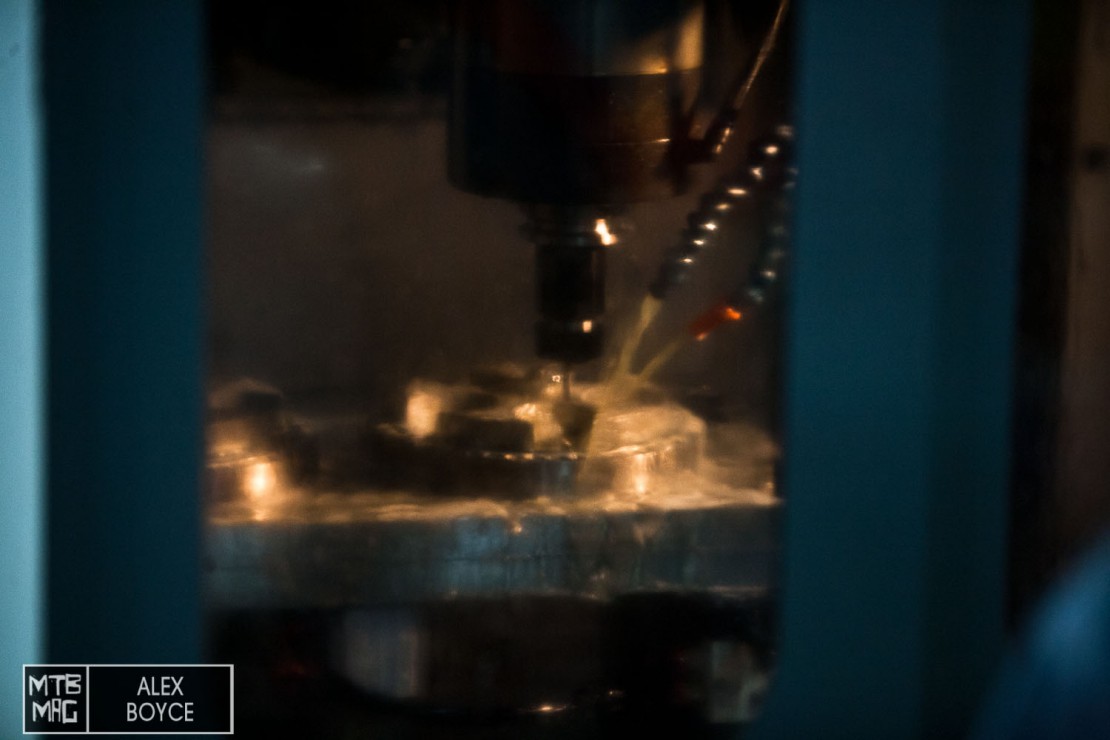
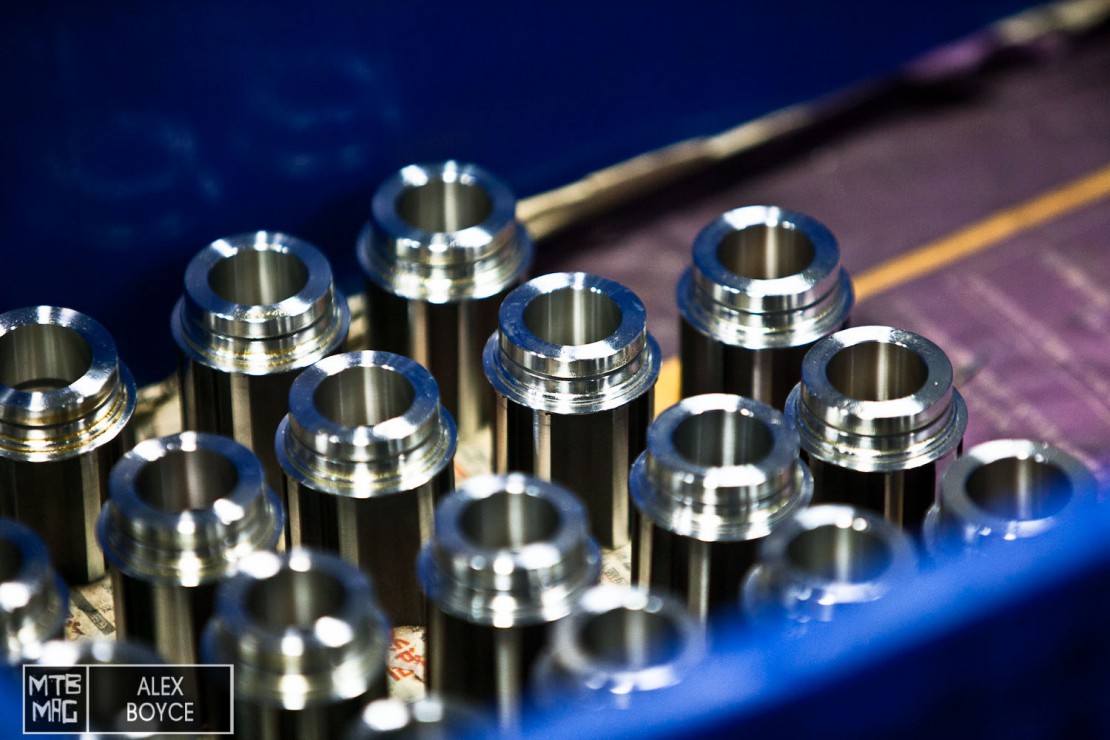
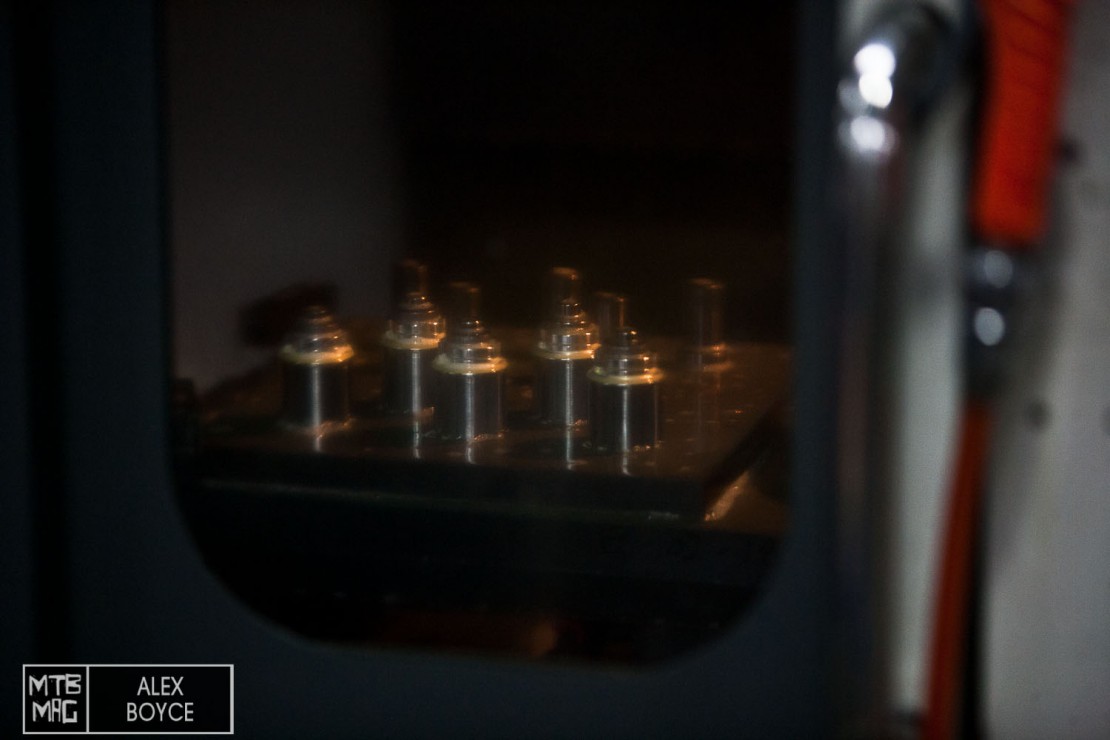
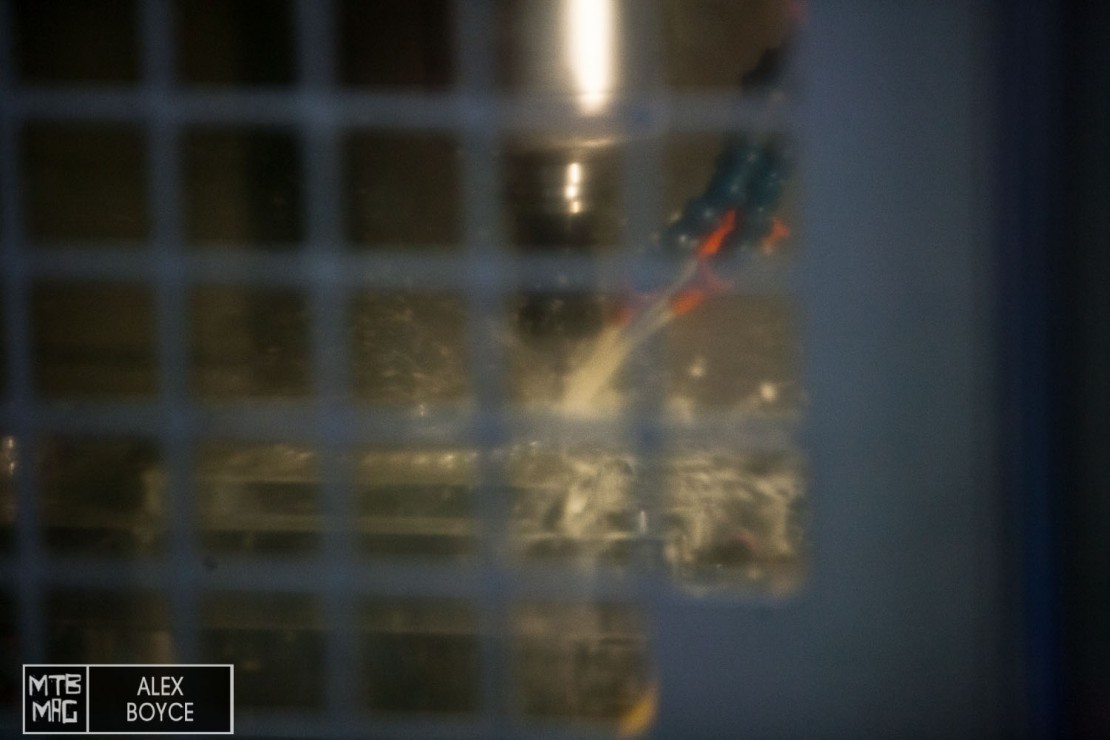
Quality Control
Taiwan has become famous over the years for being the producer of quality not just high volume. Quality control is important to maintain those factors that they are known for. TH Industries showed us a range of their facilities that they use for testing and quality control. Each test they carried out ensured that the design met the necessary extremes that our sport places on the components.
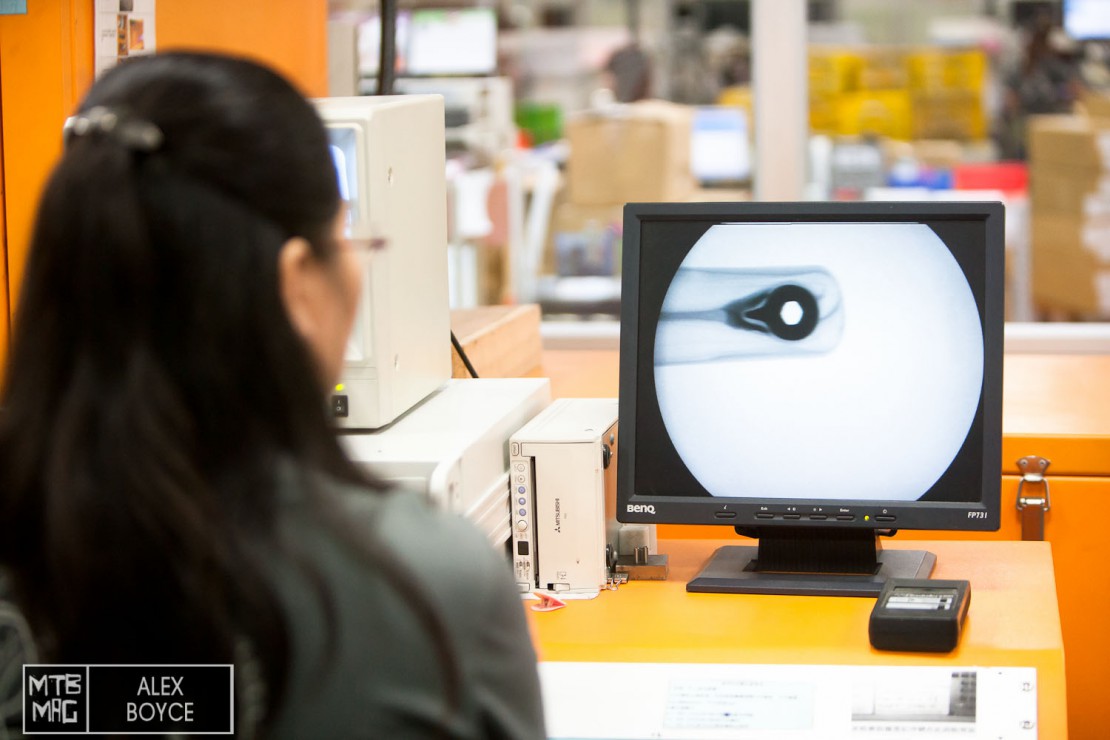
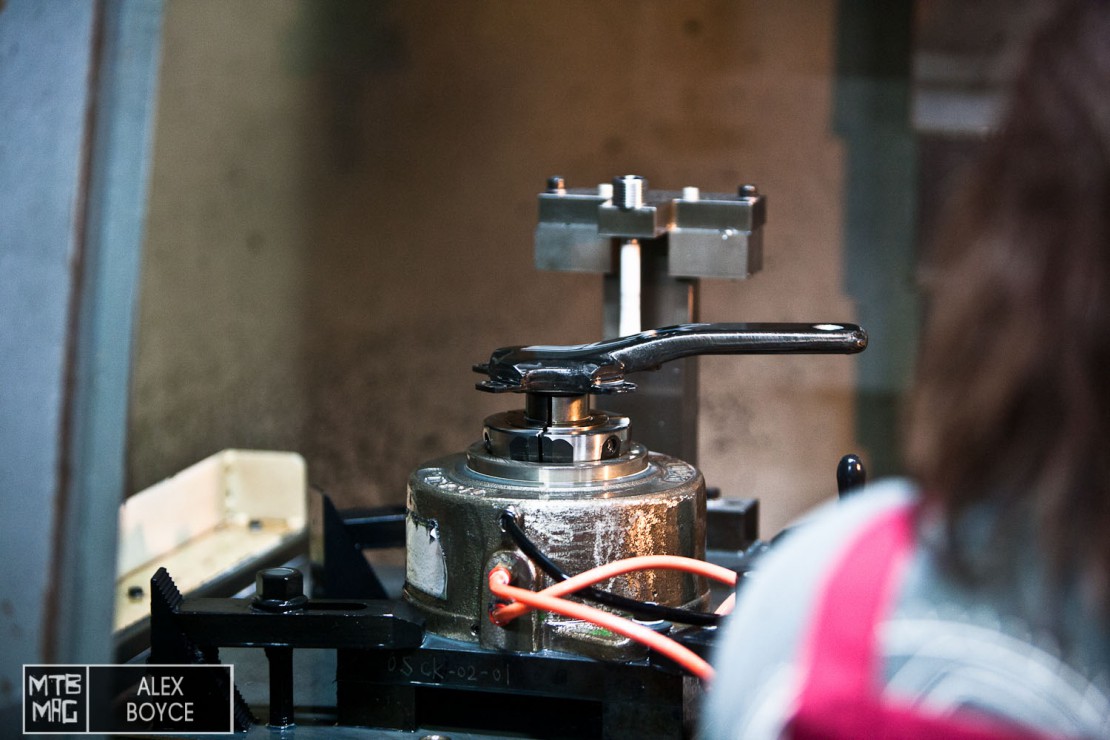
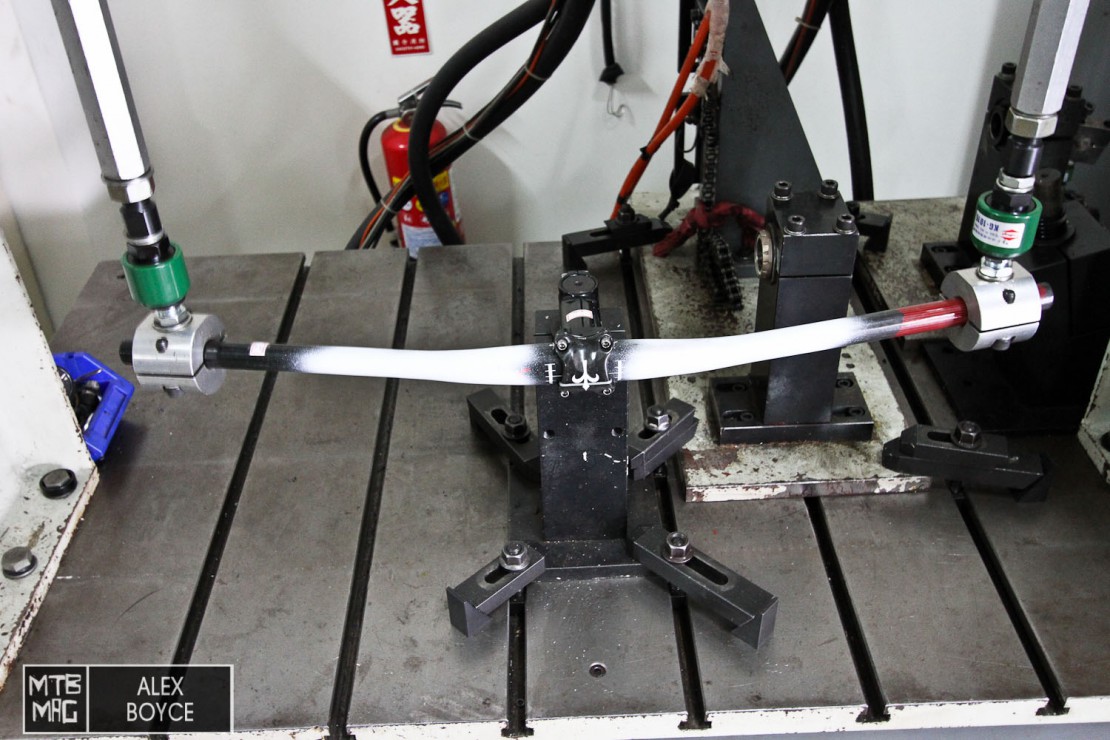
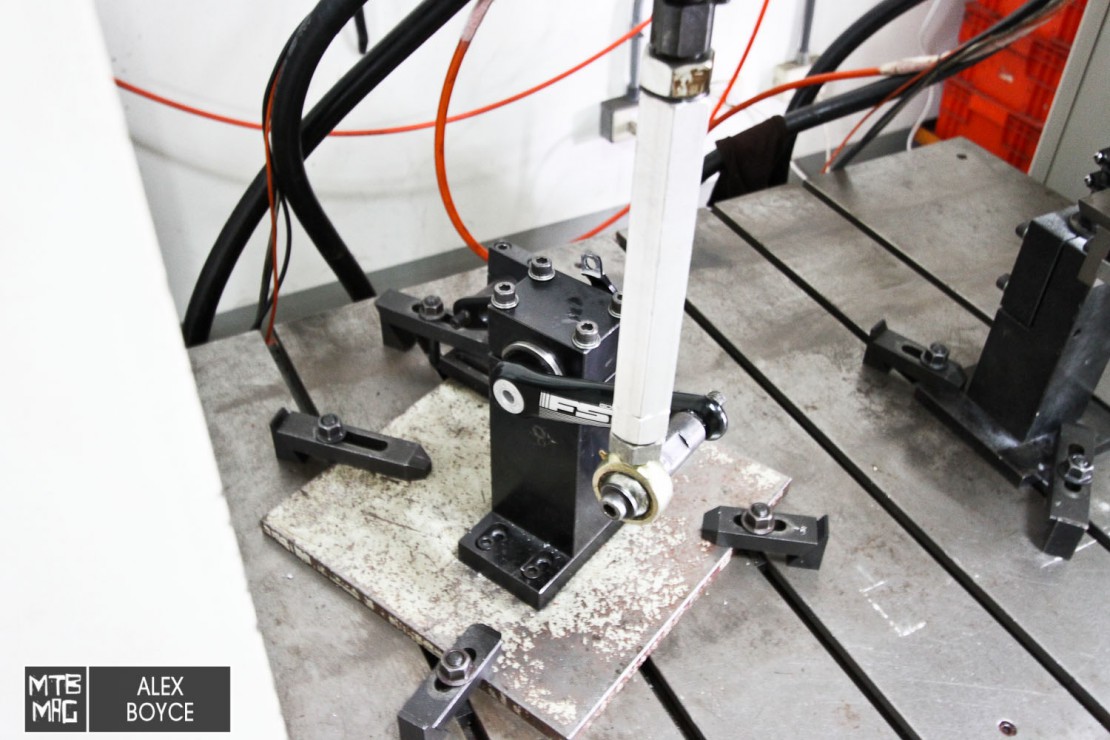
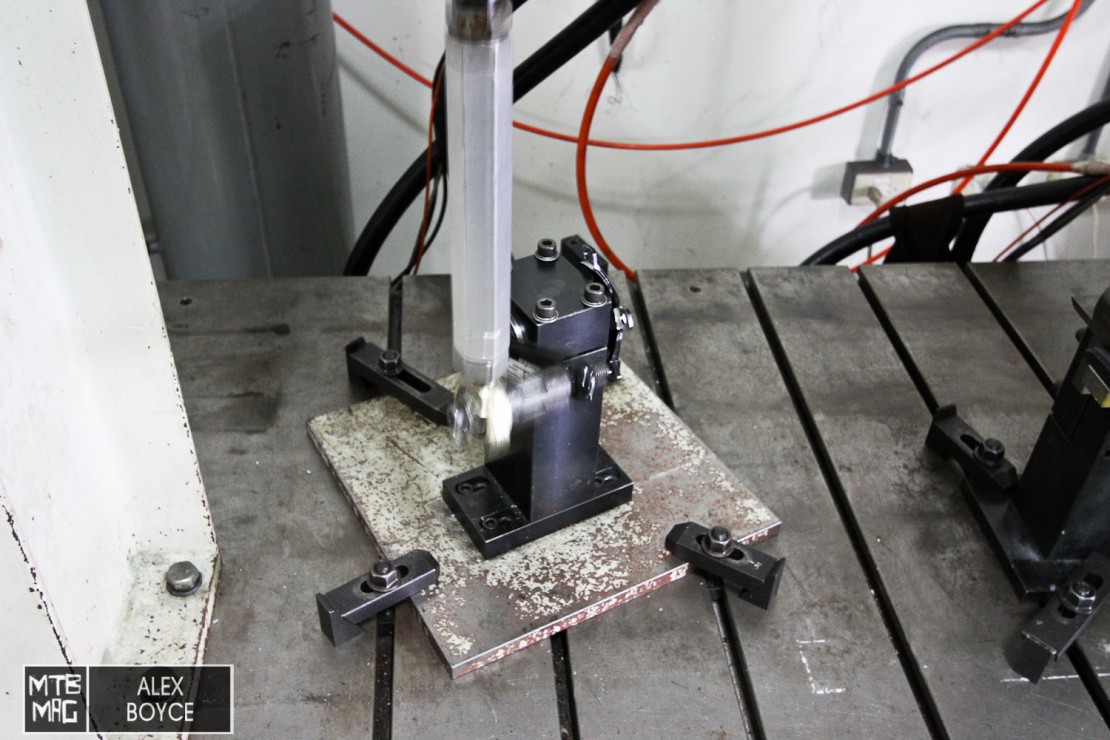
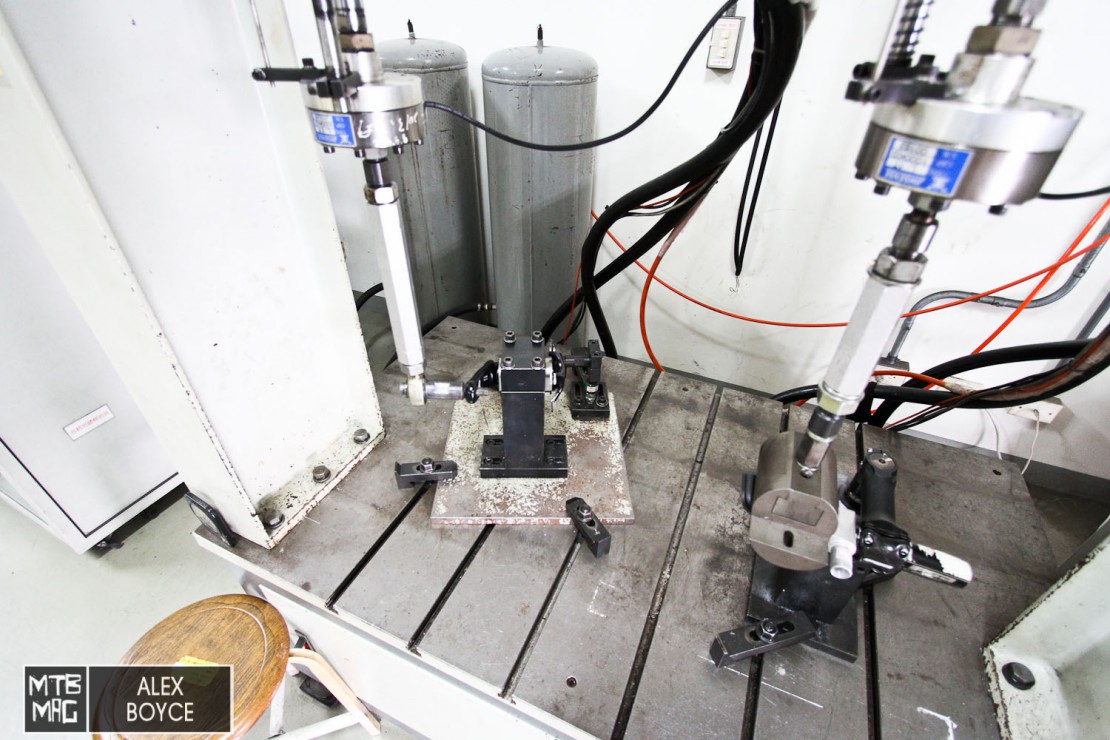
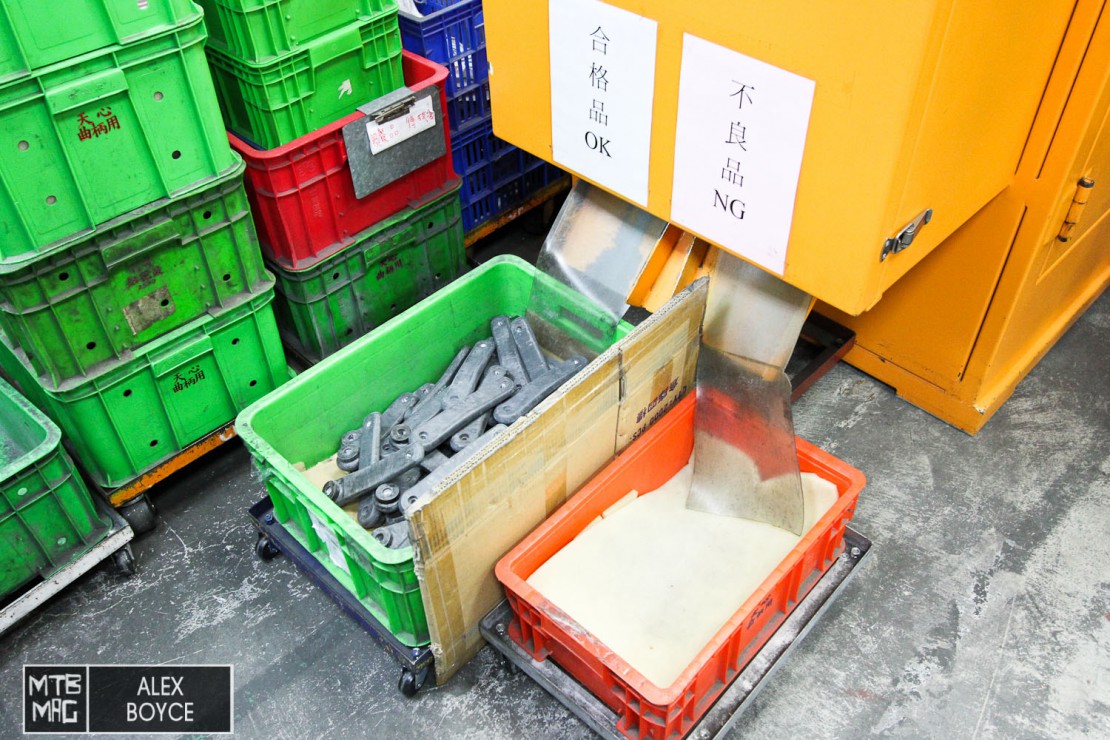
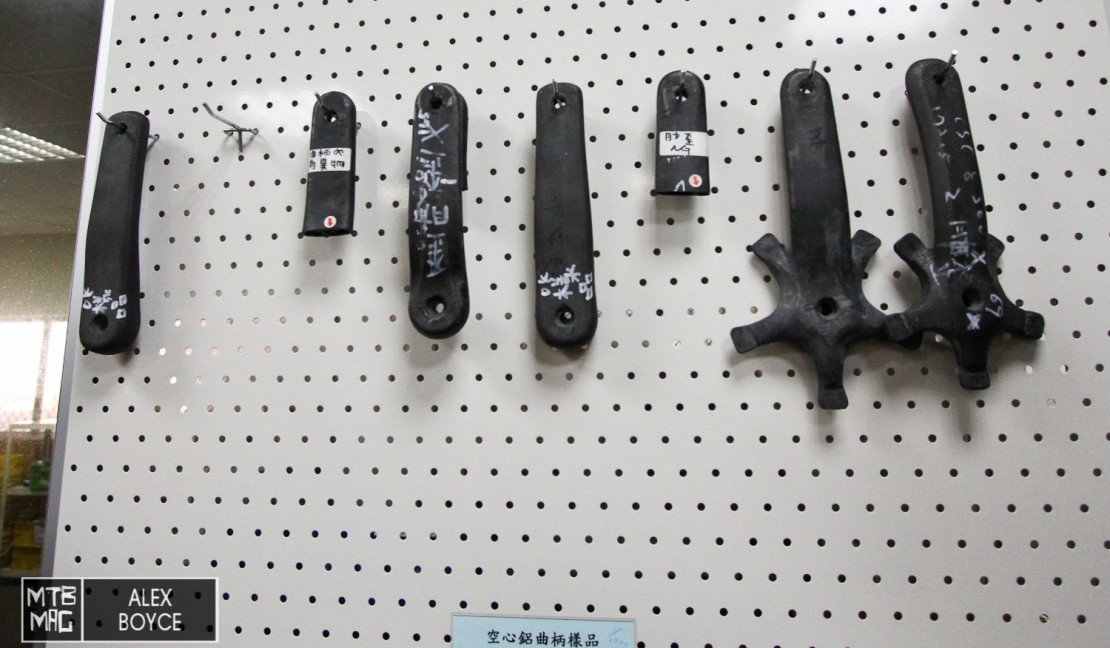
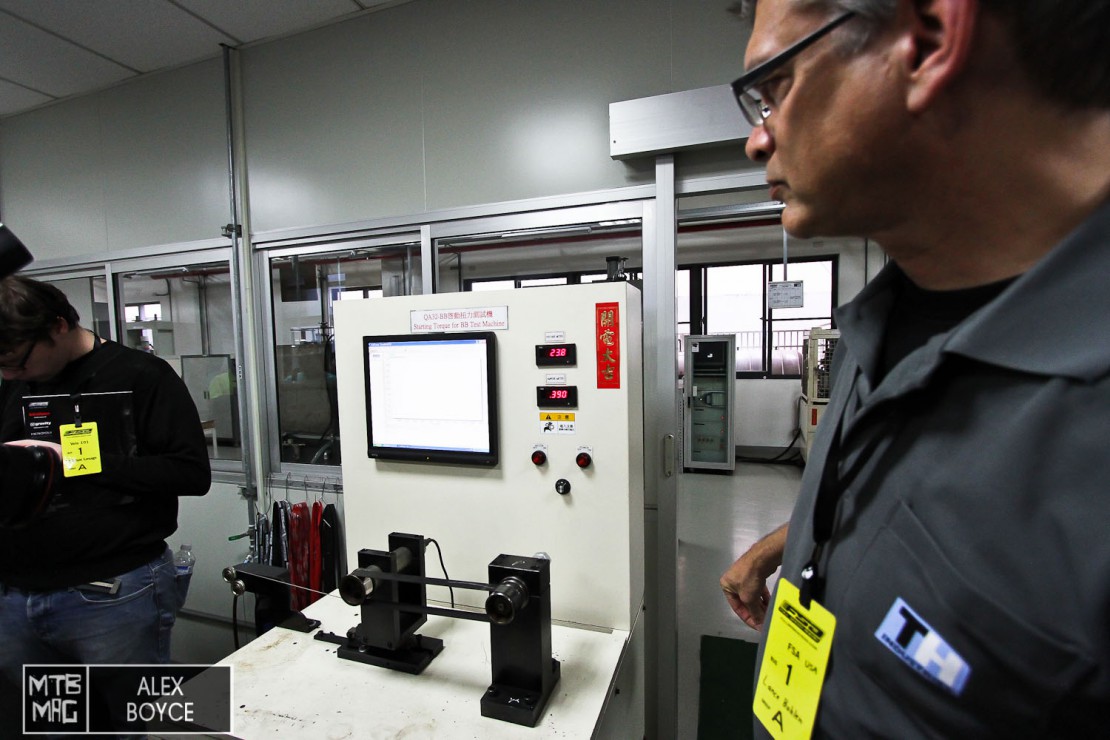
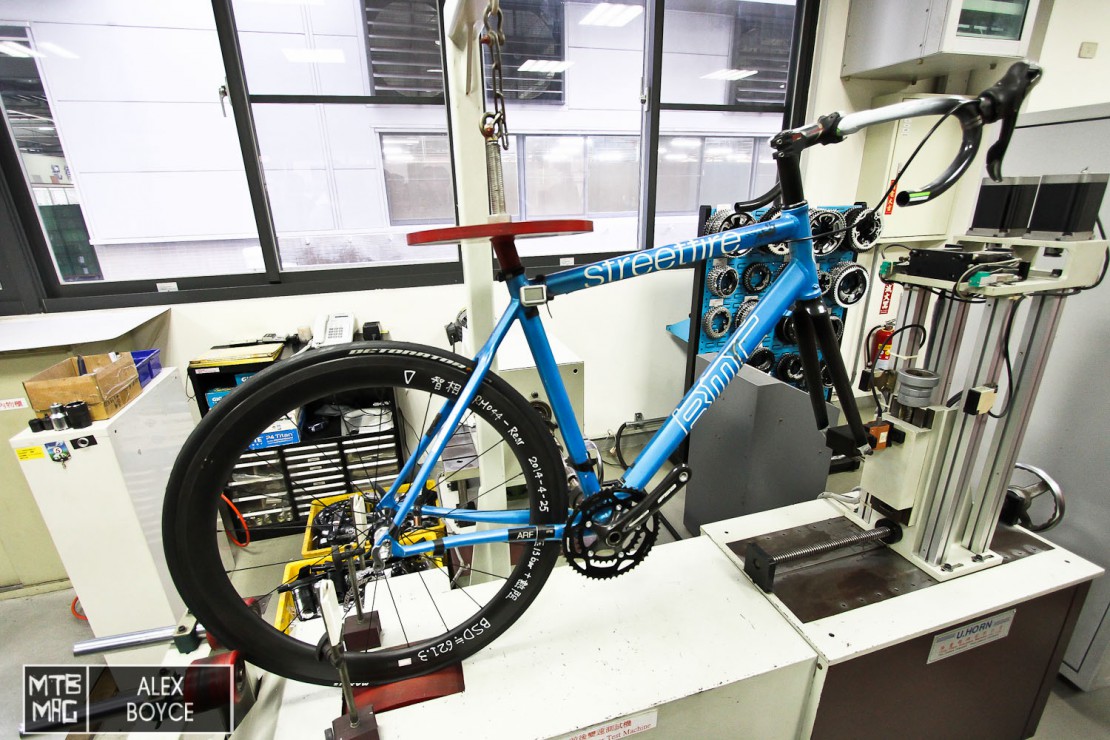
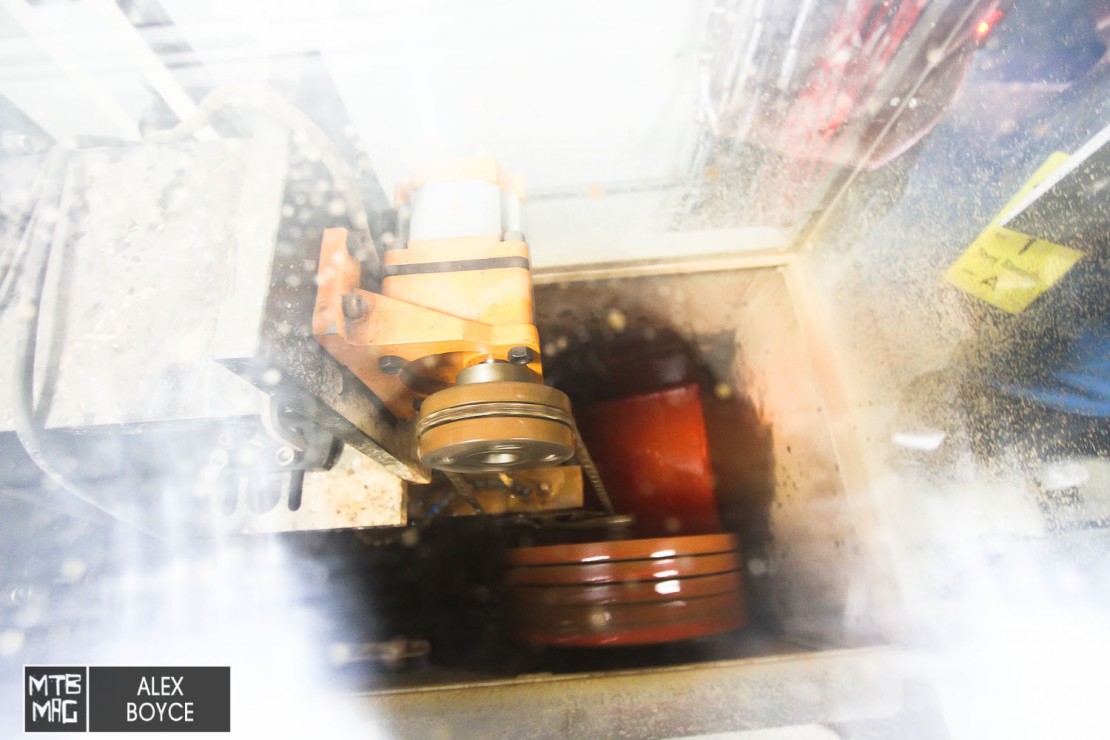
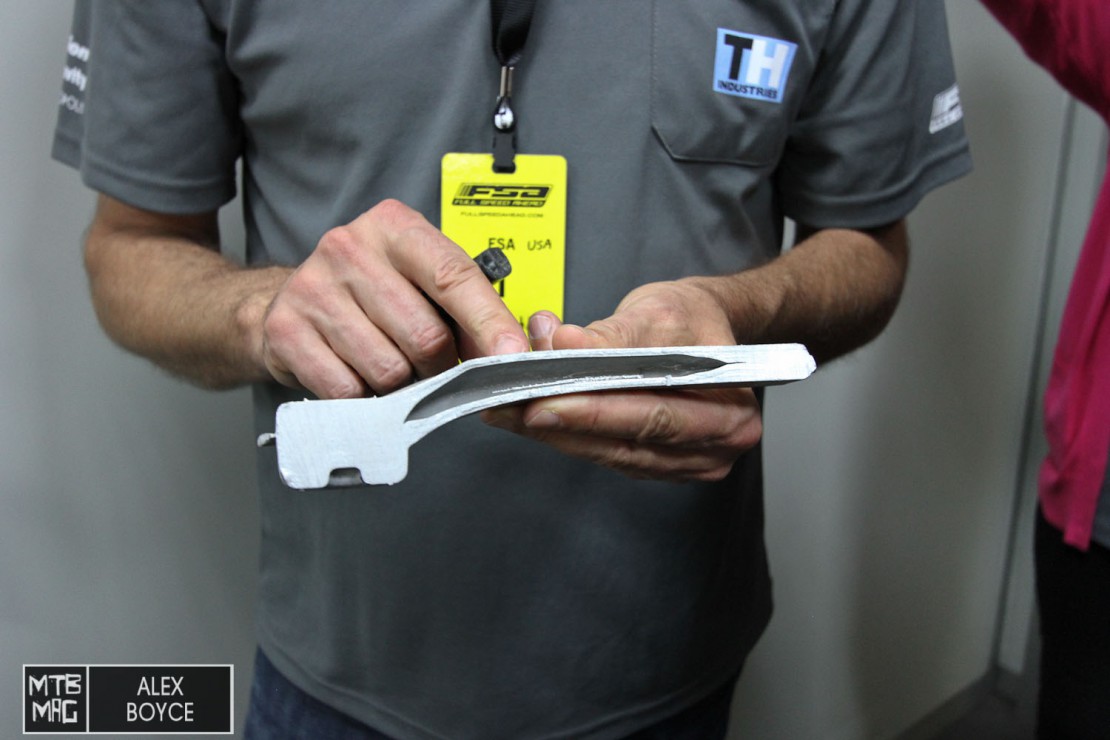
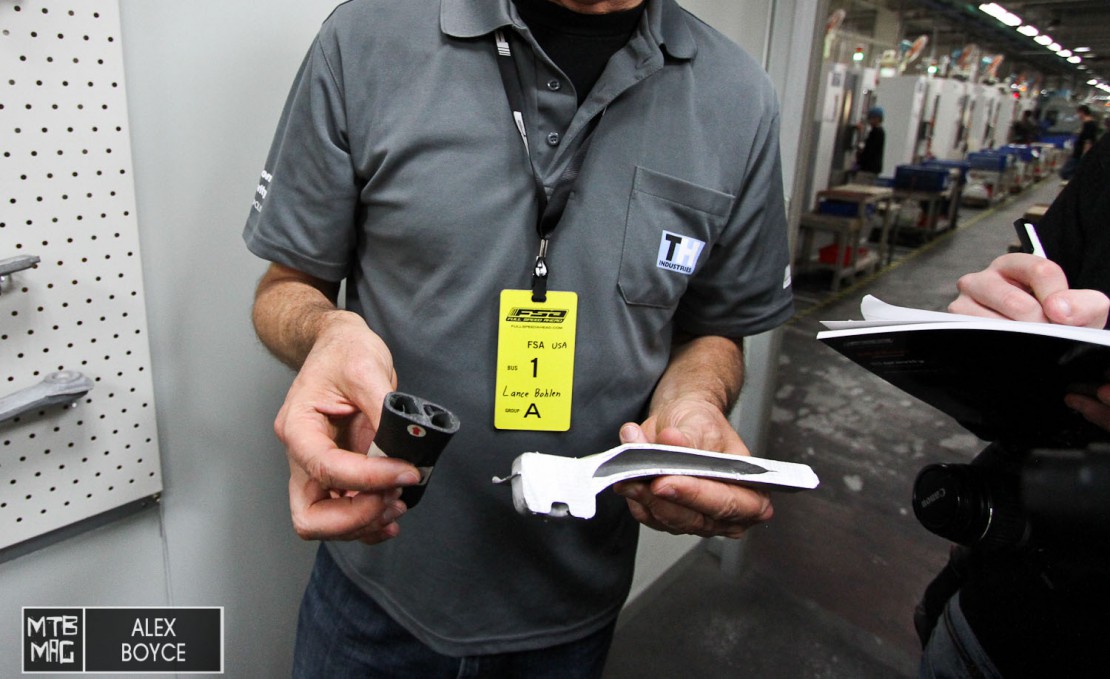
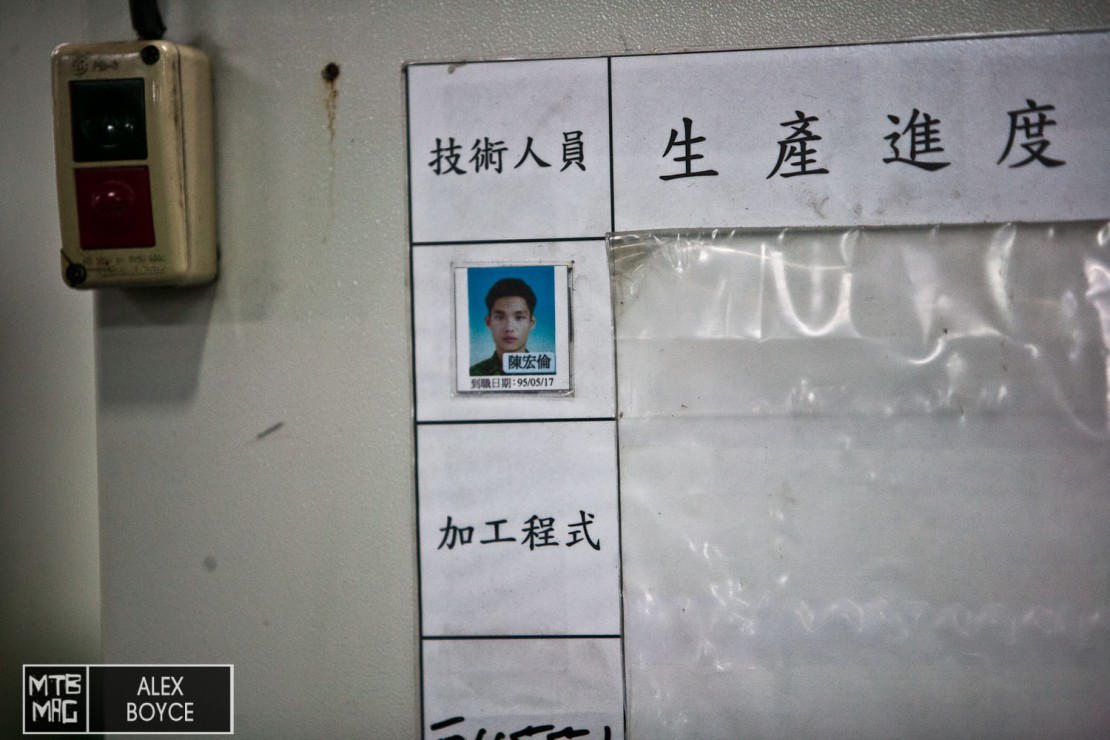
Final Products
FSA produce such a huge range of components they ship daily around the world. We had a look at their latest offerings.
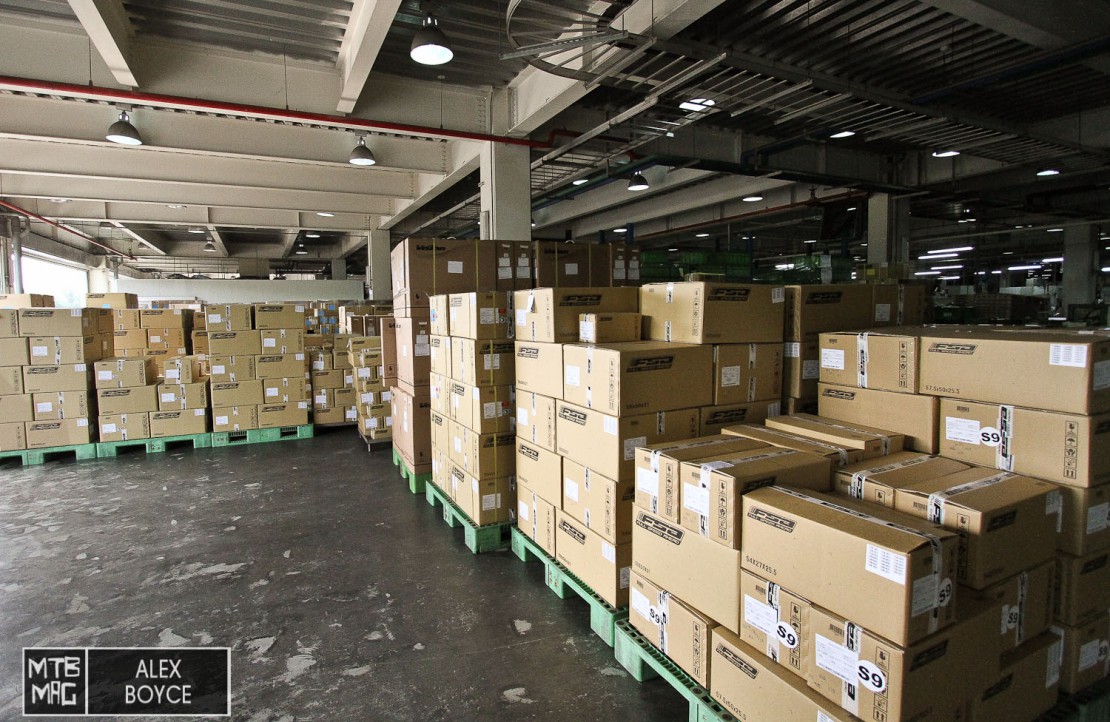
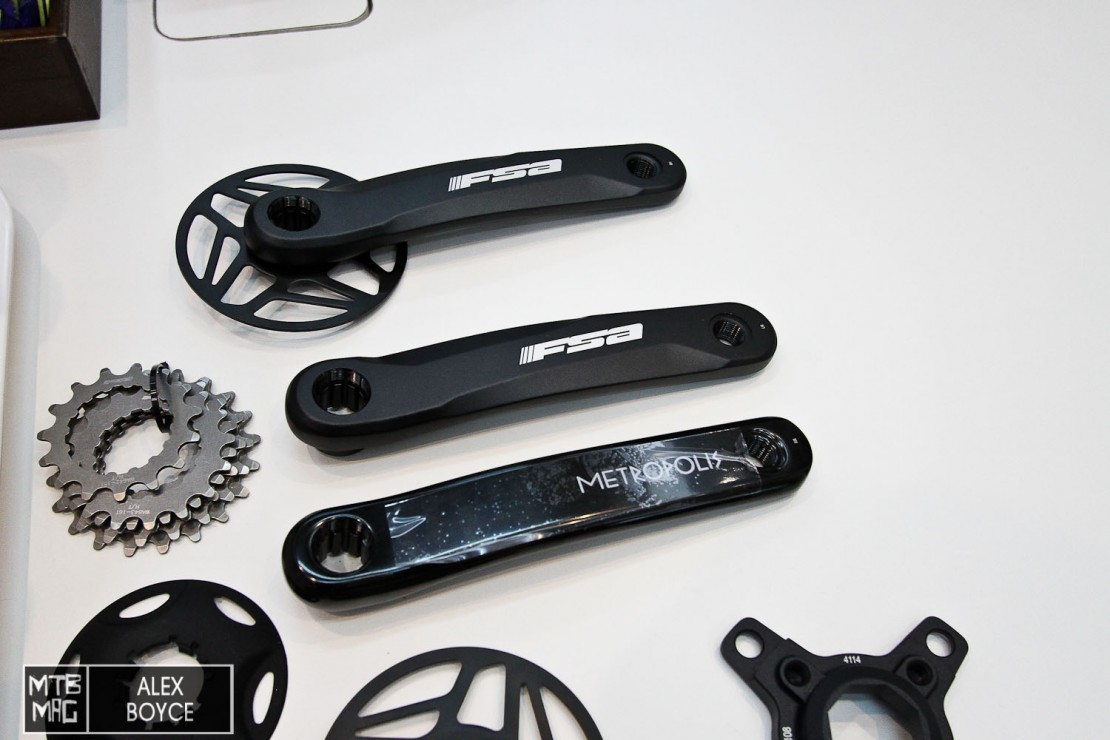
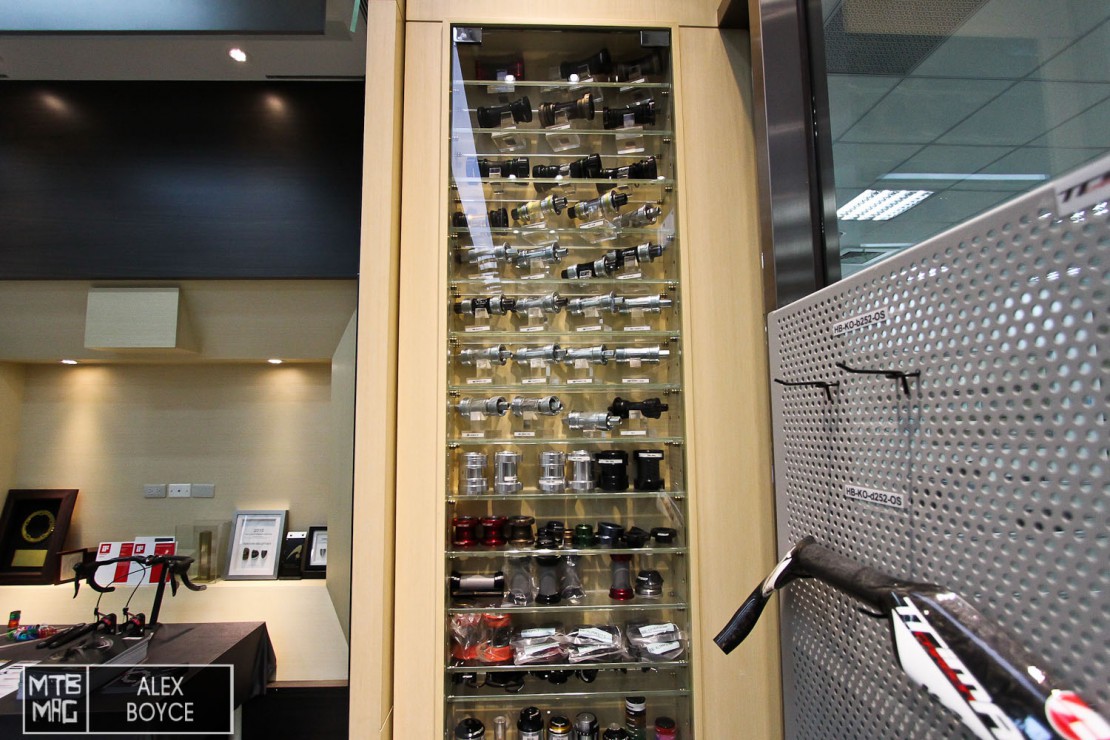
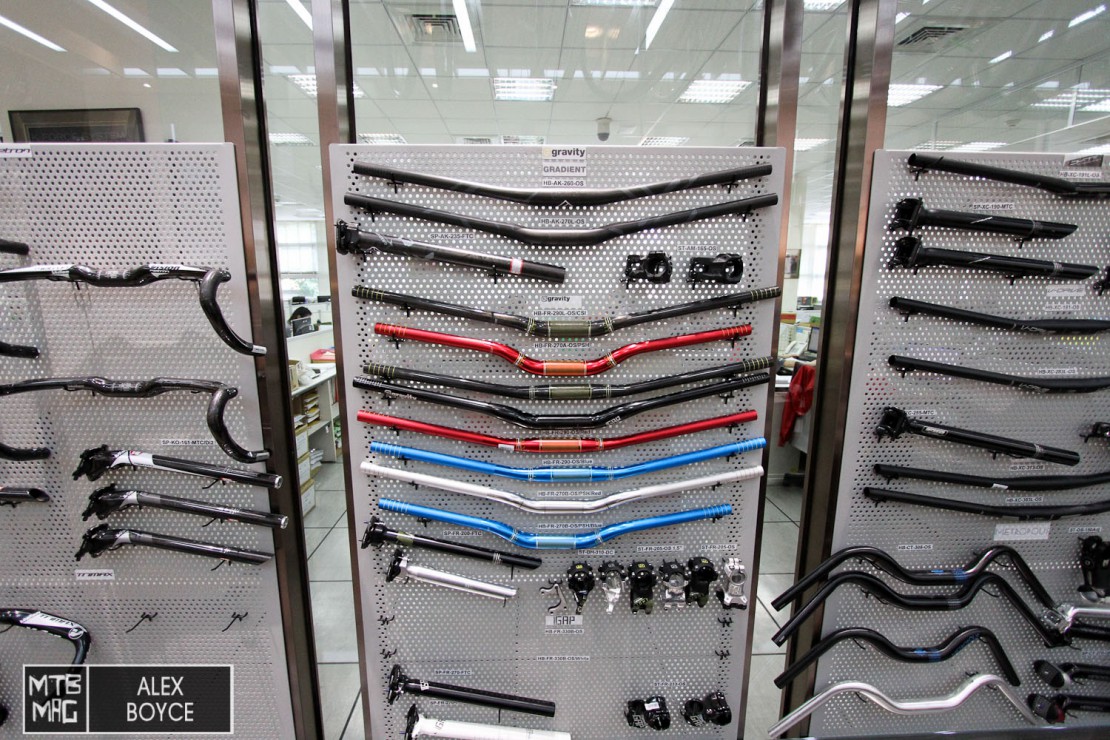
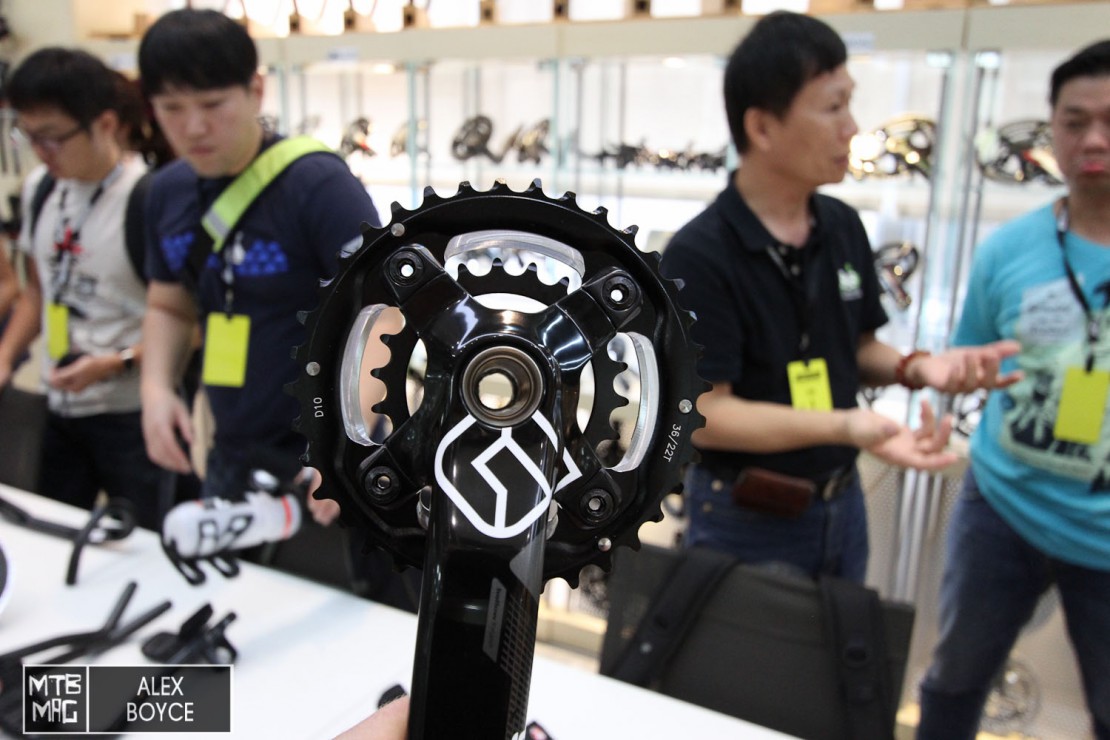
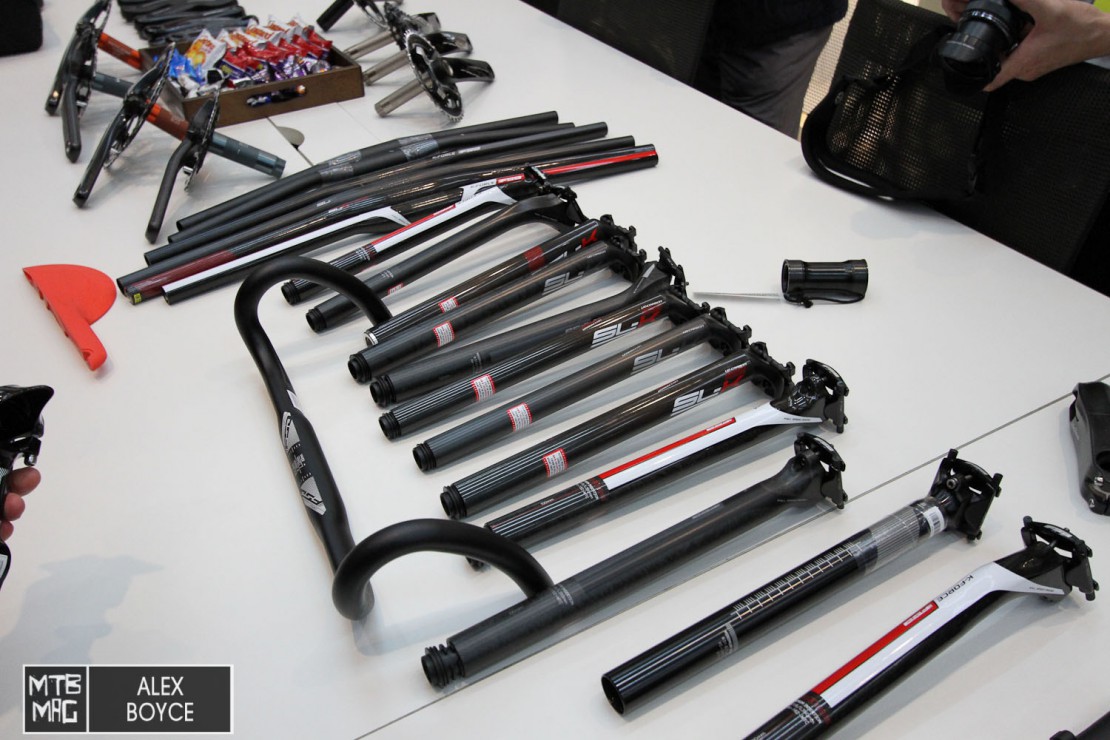
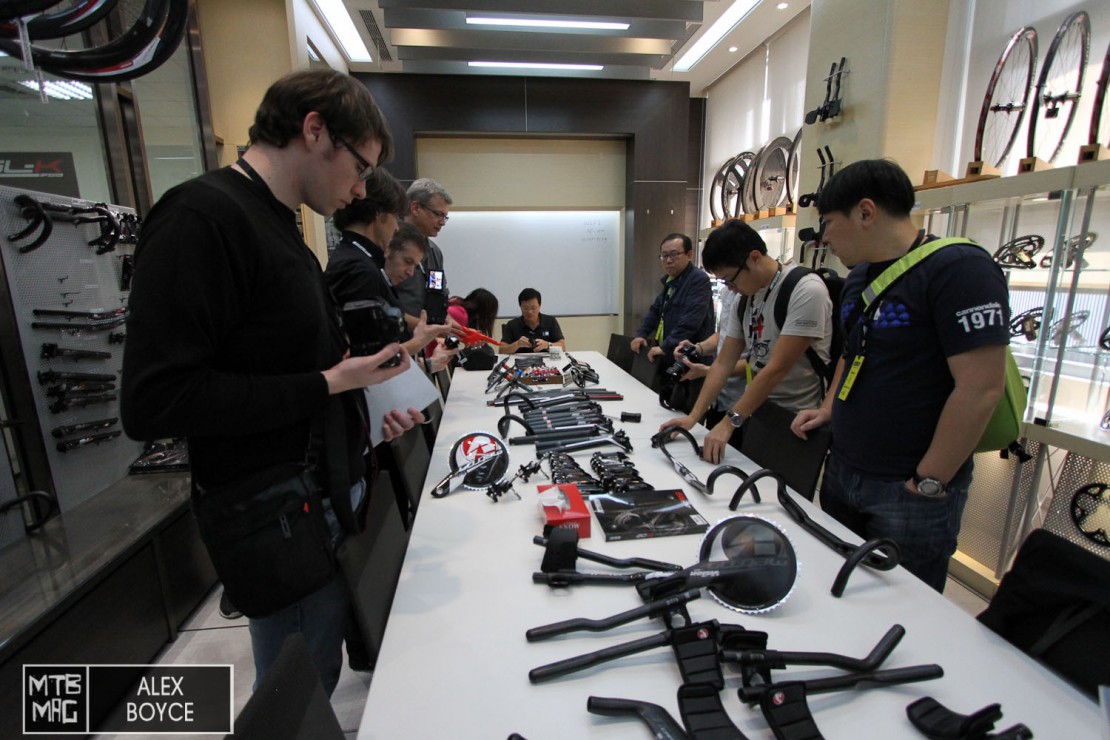
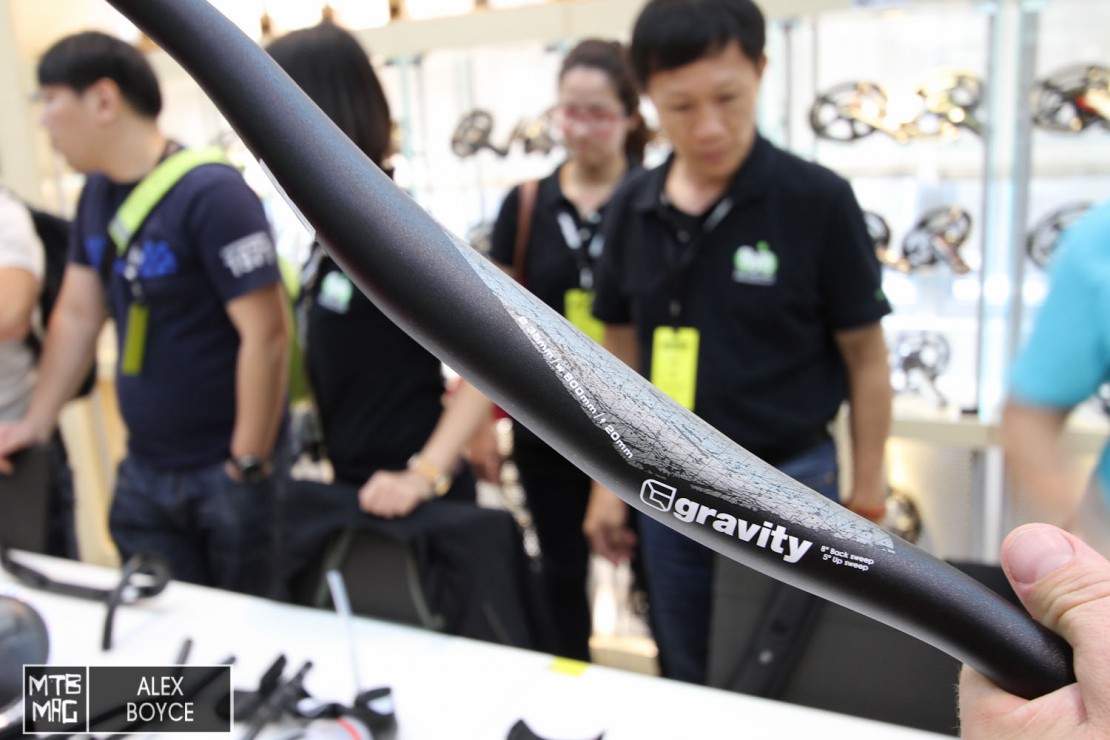
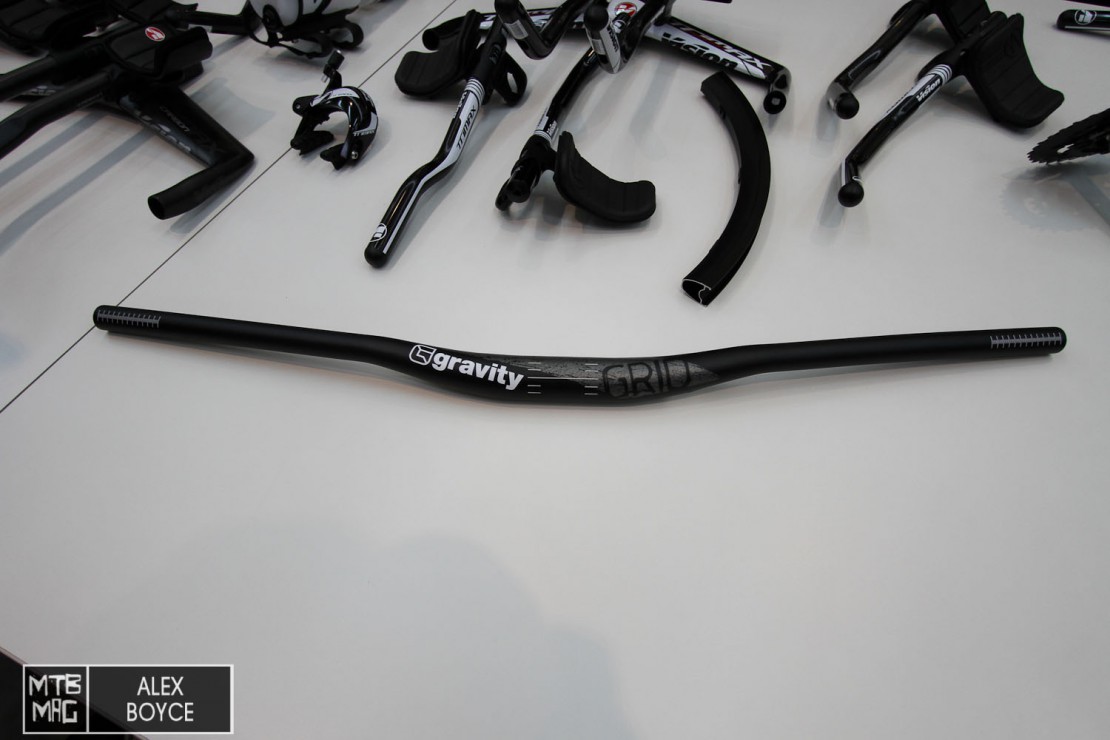
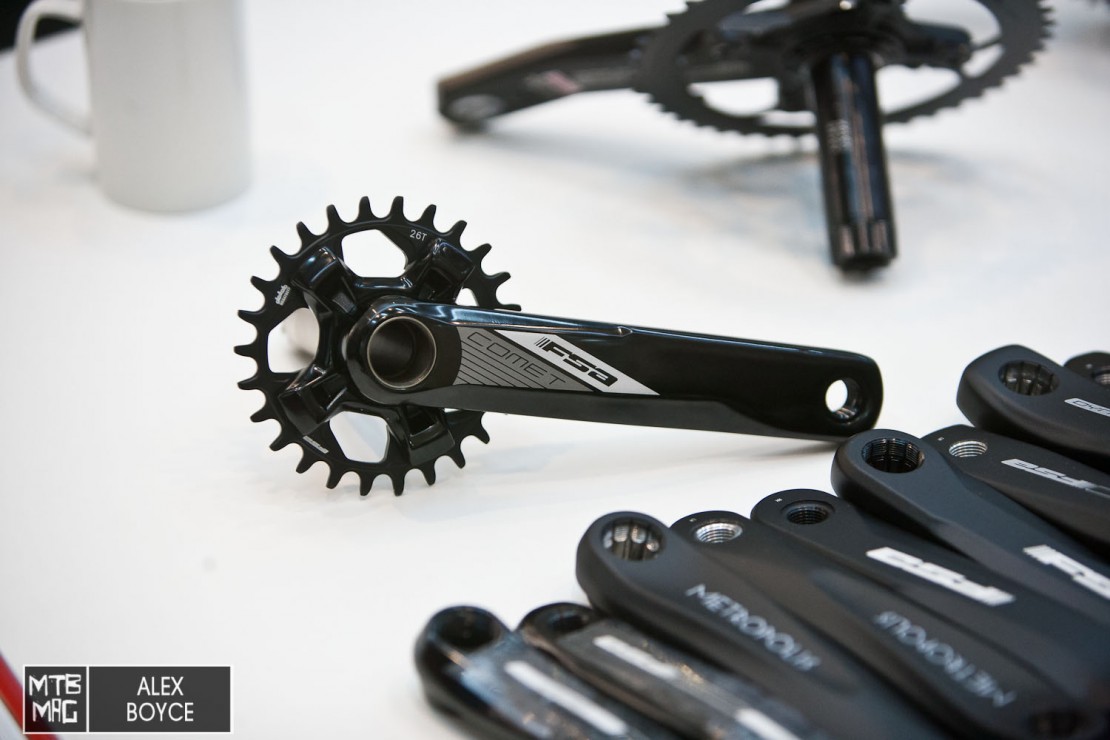
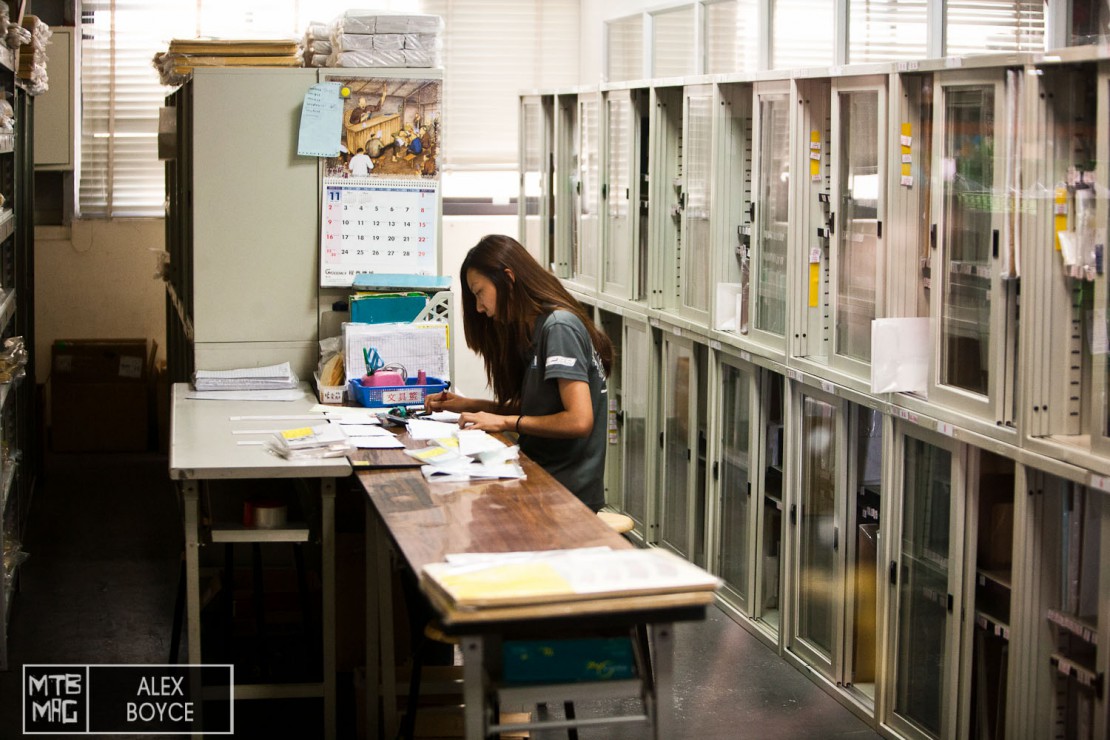
Conclusion
This was a high-tech part of our Taiwan tour but one of the most interesting, as we got to see what it takes to produce components precisely, our thanks go to FSA for their help and care in showing us around.